Лекція 17. Основні поняття та визначення теорії автоматичних систем. Класифікація систем автоматики на рухомому складі.
КЛАСИФІКАЦІЯ ЕЛЕМЕНТІВ АВТОМАТИКИ
Довгий час розвиток виробництва майже всіх продуктів був пов’язаний, в основному, з безпосереднім використанням як фізичної, так і розумової праці людини. З появою більш потужних джерел енергії, альтернативних силі м’язів людини, з’явилась можливість зменшити частку фізичної праці у процесі виробництва при одночасному підвищенні продуктивності праці шляхом використання механізмів. Цей напрямок технічного прогресу отримав назву механізації.
МЕХАНІЗАЦІЯ – напрямок технічного прогресу, спрямований на заміну фізичної роботи людини роботою механізмів і машин.
Впровадження механізації при одночасному ускладнені продуктів товарного виробництва супроводжувалось безперервним підвищенням значення функцій, які виконує людський мозок при керуванні технологічним процесом. На певному етапі розвитку промисловості саме обмеженість можливостей людського мозку при виконанні деяких операцій керування технологічним процесом (поряд з прагненням підвищення продуктивності праці і, відповідно, прибутків) обумовила новий напрямок розвитку технічного прогресу – автоматизацію.
Автоматизація – якісно нова форма удосконалення виробничого процесу, при якій машині, яка стоїть між людиною та сировиною, передається багато функцій з керування як окремими операціями технологічних циклів, так і виробничими комплексами типу цехів і навіть заводів в цілому.
Прагнення до стабілізації якості зварних з’єднань і зниження трудомісткості при їх виготовленні є і завжди було важливим стимулом до автоматизації зварювальних процесів і установок. Вже на час винаходу та практичного застосування зварювання М.М.Бенардосом та М.Г.Славяновим стан техніки та рівень розвитку науки були достатніми для переходу від ручних до механізованих та автоматизованих методів виконання цього нового технологічного процесу. Так, вже перші пристрої для механізованого зварювання запропоновані М.М. Бенардосом (1881 р.), включали автоматичні регулятори дуги з графітовим електродом.
М.Г.Славянов (1888 р.) прямо вказував, що тільки наявність автоматичних регуляторів дуги може забезпечити реальну можливість промислового застосування дугового зварювання плавким електродом. Розвиток зварювання як механізованого і навіть автоматизованого процесу з початку його виникнення не є випадковістю. Зварювання, як потужний енергетичний процес, що визначається високими параметрами, не могло б успішно розвиватись, якби базувалось тільки на вмінні та особистих якостях оператора-зварника, через те, що фізичні данні та психологічні особливості людини просто недостатні для керування швидкоплинними процесами з високими енергетичними характеристиками. Тому застосування засобів механізації та автоматизації дугового зварювання вже на перших етапах його розвитку виявилось закономірним і пов’язаним з об’єктивними особливостями цього нового технологічного процесу.
АВТОМАТИЗАЦІЯ — напрямок технічного прогресу, спрямований на заміну розумової праці людини роботою самодіючих систем, що виконують операції технологічного процесу виготовлення продукції без безпосередньої участі людини.Автоматизація нерозривно поєднана з механізацією і є, по суті, її вищою формою. Автоматизація, виводячи людину із сфери керування виробничими процесами, суттєво змінює роль людини у виробництві, що дозволяє розглядати автоматизацію як якісно нову форму удосконалення виробничих процесів. Автоматизація полягає у впровадженні у виробничий процес автоматів у виробництві.
АВТОМАТ – пристрій, що виконує деякий процес без безпосередньої участі людини.
Використання автоматів зафіксовано ще в стародавні часи. Це були іграшки, мисливські, військові та охоронні пристрої. Широке використання в промисловості автомати набули тільки у другій половині 18-го сторіччя у зв’язку з прагненням власників мануфактур збільшити свої прибутки шляхом зменшення частки людської праці у виробництві товарів. Тільки в 40-50х роках 20-го сторіччя автомати почали застосовувати для вирішення суто задач керування, які до того часу були виключно у компетенції людини. Розрізняють автоматизовані та автоматичні системи керування.
АВТОМАТИЧНІ СИСТЕМИ КЕРУВАННЯ – системи керування, що функціонують без безпосередньої участі людини.
АВТОМАТИЗОВАНІ СИСТЕМИ КЕРУВАННЯ – системи керування, в яких, як обов'язковий елемент, бере участь людина-оператор.
Предметом автоматизації можуть бути як окремі етапи технологічного процесу або обслуговування установок (часткова автоматизація), так і увесь технологічний процес (комплексна автоматизація). Теоретичні засади побудови як автоматичних, так і автоматизованих систем надає наукова дисципліна, що має назву кібернетика.
КІБЕРНЕТИКА (з грецької – мистецтво керувати) – наука про загальні закони керування, отримання, зберігання, передачу і перетворення інформації в складних керуючих системах.
Термін "кібернетика" вперше (після давніх греків) вжив у 1834 видатний французький вчений Андре Мари Ампер (1775-1836) у запропонованій ним класифікації наук для позначення науки про керування людським суспільством, якої на той час ще не існувало. Після Ампера цей термін було забуто і знов відроджено американським вченим Н.Вінером (1894-1964) у назві опублікованої ним в 1948 році книги. Цю дату прийнято вважати датою народження кібернетики як самостійної науки. Н.Вінер визначив кібернетику як "науку про керування і зв’язок в тварині і машині". Людське суспільство випало з цього визначення. В 1954 році, відчуваючи цей недолік, Н. Вінер видав нову книгу "Кібернетика та суспільство". По суті ці книги ще не містили послідовного викладення методів нової науки і її результатів. Однак ідеї, що містились в цих книгах, стали могутнім поштовхом для розвитку нової науки в усьому цивілізованому світі.Основною задачею теоретичної кібернетики є розробка апарату і методів дослідження, що придатні для вивчення систем керування, незалежно від їх природи. Теоретична кібернетика містить у собі ряд наукових напрямків, що розвинулись раніше в деяких розділах математики (математична логіка, теорія ймовірностей, теорія ігор та інші) та наукові напрямки, що розвинулись вже безпосередньо в межах самої кібернетики (теорія автоматів, теорія формальних граматик, теорія розпізнавання образів та інші).
Окрім теоретичного ядра, в кібернетиці виникли і сформувались як самостійні різноманітні прикладні напрямки. Так проблеми автоматизації технологічних процесів, керування складними технологічними комплексами сформувались в окремий напрямок, що називається технічна кібернетика.
ТЕХНІЧНА КІБЕРНЕТИКА - напрям кібернетики, в якому вивчаються на основі загальних для кібернетики в цілому наукових ідей і методів технічні системи керування.
Технічна кібернетика є сучасним етапом розвитку теорії та практики автоматичного регулювання та керування, а також науковою базою для вирішення задач комплексної автоматизації виробництва, транспортних та інших складних систем керування. Складні системи керування – це узагальнююча назва систем, що складається з великої кількості взаємопов'язаних елементів. Часто складними системами називають системи, що неможливо описати коректно математично або тому, що система містить велику кількість різних елементів, які пов'язані між собою невідомим чином, або тому, що невідома природа явищ, які відбуваються в системі і тому їх неможливо кількісно описати. Одною зі складових технічної кібернетики є теорія автоматичного керування (теорія автоматичного регулювання), яка сформувалась в самостійну наукову дисципліну приблизно в 1940 році.
ТЕОРІЯ АВТОМАТИЧНОГО КЕРУВАННЯ — розділ технічної кібернетики, що вивчає системи автоматичного керування різної природи та складності.Узагальнюючий підхід до вивчення процесів керування потребує певної абстракції від природи і конструктивних особливостей складових частин систем автоматичного керування. Саме тому замість реальних об’єктів у теорії автоматичного керування розглядаються адекватні їм математичні моделі.
МАТЕМАТИЧНА МОДЕЛЬ — система математичних співвідношень, які описують суттєві властивості системи або процесу, що вивчається.
Теорія автоматичного керування (ТАК) на сучасному етапі розвитку ототожнюється з теорією автоматичного регулювання (ТАР), яку у свій час вважали окремою науковою дисципліною. Однак і ТАК і ТАР завжди використовували спільну термінологію, а самі поняття "керування" і "регулювання" у науковій літературі в багатьох випадках використовувались (і використовуються нині) як синоніми. Хоча слід зазначити, що і тепер ще інколи розрізняють ці поняття як окремі. Дамо визначення цих понять.
АВТОМАТИЧНЕ КЕРУВАННЯ — сукупність дій, які спрямовані на здійснення технологічного процесу або операції за певним законом без безпосередньої участі людини.
АВТОМАТИЧНЕ РЕГУЛЮВАННЯ— сукупність дій, які спрямовані на зміну за заданим законом якоїсь одної фізичної величини в технологічному процесі, що виконується без участі людини.
В такому сенсі "автоматичне керування" є більш загальним поняттям і відносно якого "автоматичне регулювання" займає підлегле положення. Наприклад, автоматичне керування процесу контактного точкового зварювання вимагає за короткий термін процесу, який вимірюється долями секунди, вмикання та вимикання в суворо визначені моменти часу приводу стиснення електродів, регулювання зварювального струму з метою його зміни за певним законом в умовах можливих змін напруги живильної мережі, шунтування струму, тощо. Розглянемо узагальнену схему системи керування без огляду на її фізичну сутність. Процес або пристрій, що його здійснює, розглядають як об'єкт керування (об'єкт) О (рис.1.1)
Рисунок 1.1 - Формалізоване представлення процесу керування
Стан об'єкту характеризується сукупністю вихідних фізичних величин (параметрів або координат), які в наслідок процесу керування мають набути заданих значень. Ці величини мають назву "керовані величини" або "регульовані величини" Yj(t).
Стан об'єкта визначається поточними внутрішніми процесами, на які впливають зовнішні фактори - дії Xi(t), Zm(t) - вхідні змінні (або функції, сигнали), точки прикладання яких називають входами.
Ті вхідні параметри (фізичні величини) Xi(t), які дають інформацію про задачі керування (задаються людиною-оператором або керуючим пристроєм) називають задавальними діями або завданням.
Зовнішні дії Zm(t) на об'єкт, які порушують встановлений зв'язок між завданням Xi(t) і вихідними параметрами Yj(t) називають збуреннями (перешкодами).
Керуючий пристрій виконує основні функції управління, шляхом вироблення керуючого впливу Xрki(t) в залежності від помилки (відхилення), тобто Xрki(t) = f[Yj(t)- Xi(t)]. Закон регулювання визначає вид цієї залежності без урахування інерційності елементів регулятора. Закон керування визначає основні якісні та кількісні характеристики систем.
Розрізняють лінійні і нелінійні закони керування. Крім того, закони регулювання можуть бути реалізовані в безперервному вигляді або у цифровому. Цифрові закони регулювання реалізуються шляхом побудови регуляторів за допомогою засобів обчислювальної техніки.
АВТОМАТИЧНОЮ СИСТЕМОЮ КЕРУВАННЯ (системою автоматичного керування САК, або системою автоматичного регулювання САР) називають сукупність об'єкта О керування (або регулювання) і технічних керуючих пристроїв КП, які взаємодіють з об'єктом відповідно до закону (алгоритму) керування (рис.1.2).
АЛГОРИТМ КЕРУВАННЯ – сукупність правил, які визначають характер керуючих дій на об'єкт О.
АЛГОРИТМ ФУНКЦІОНУВАННЯ - сукупності правил, що визначають хід виконання технологічного процесу (в об'єкті, установці).
Рисунок 1.2 -Формалізоване представлення системи автоматичного керування
Керувати об'єктом О означає виробляти керуючі дії Xрki(t) із таким розрахунком, щоб регульовані параметри Yj(t) змінювались за законами, що задаються завданнями Xi(t), незалежно від дії на об'єкт координатних Zm(t) та параметричних Fn(t) збурень. Індекси i, j, k, m, n позначають кількість відповідних дій та параметрів. Регулювання – це, по суті, керування простими об'єктами з одним вихідним параметром Xр(t) і, відповідно, однією задавальною дією Xз(t) та однією керуючою дією Yк(t), яка виробляється регулятором (КП). Керуючий пристрій у цьому випадку часто називають регулятором.
Далі
КЛАСИФІКАЦІЯ СИСТЕМ АВТОМАТИЧНОГО КЕРУВАННЯ
Класифікація систем автоматичного керування може здійснюватись за ознаками, що відбивають певні особливості системи (табл.1.1). Запропонована класифікація систем автоматичного керування не є вичерпною і єдиною можливою. Як будь-яка класифікація, вона представляє певні уподобання автора, хоча і ґрунтується на найбільш часто застосованих термінах і поняттях.
Таблиця 1.1.
Системи автоматичного керування
|
За складністю системи керування
| |||
одномірні
|
багатомірні
|
складні
| ||
зв'язні
|
не зв'язні
| |||
За метою керування
| ||||
стабілізації
|
програмного керування
|
стеження
|
екстремальні
| |
За властивостями
| ||||
лінійні
|
не лінійні
|
стаціонарні
|
не стаціонарні
| |
За характером протікання інформаційних процесів
| ||||
неперервні
|
дискретні
| |||
релейні
|
імпульсні
|
цифрові
| ||
За характером причинно-наслідкових зв'язків
| ||||
замкнуті
|
розімкнуті
|
ОДНОМІРНІ СИСТЕМИ — це системи, стан яких визначається одним вихідним параметром і однією вхідною дією(рис. 1.7).
Рисунок 1.7 - Одномірна система
У більшості випадків застосовують одновимірні автоматичні установки - САР, у яких регулюється тільки один параметр - напруга, довжина дуги, струм, швидкість, рівень рідкого металу, та інші. Відповідно використовується тільки одна керуюча дія - напруга керування фазоімпульсним блоком, струм підмагнічування обмотки збудження генератора або магнітного підсилювача, напруга живлення якоря двигуна і т. ін.
БАГАТОВИМІРНІ СИСТЕМИ — це системи, стан яких визначається багатьма вихідними параметрами і (або) багатьма вхідними діями (рис.1.8).
Рисунок 1.8 - Багатовимірні системи керування
Реальні зварювальні процеси і установки є багатовимірними, оскільки технологічний режим визначається значною кількістю взаємопов'язаних параметрів. При одному контрольованому параметрі такі системи можуть мати декілька регулюючих елементів, кожний з яких діє на один і той же об'єкт. Так, для керування режимом дугового зварювання необхідно регулювати швидкість подавання електродного дроту, довжину дуги і швидкість зварювання. У випадку зварювання швів складної конфігурації, кількість регульованих величин може досягати шести та більше. Електронно-променева установка вимагає регулювання понад десяти параметрів. Складність керування зростає пропорційно квадрату кількості регульованих параметрів. При цьому необхідно враховувати взаємозалежність та взаємопов'язаність регульованих параметрів.
НЕ ЗВ'ЯЗНА СИСТЕМА — це система, яка містить кілька самостійних керуючих пристроїв (локальних регуляторів), кожний з яких керує однією, незалежною від інших регульованих параметрів, величиною (рис. 1.9). Тобто мають два і більше замкнутих контурів передачі дії. Такі системи використовують, наприклад, в САК ЕПЗ. Однак реальної незалежності роботи регуляторів досягнути важко тому, якщо всі вони виявляються пов'язаними через об'єкт. Дія кожного регулятора на об'єкт призводить до зміни всіх його параметрів і якість регулювання в цілому виходить низькою.
Рисунок 1.9 - Не зв'язна система
ЗВ'ЯЗНА СИСТЕМА — це система, яка містить внутрішні зв'язки між регульованими величинами (). Прикладом такого об'єкту керування є звичайні установки дугового зварювання плавким електродом. У них вимагається керувати двома параметрами: середнім струмом Ід і середньою довжиною дуги Lд. Керуючими діями є напруга джерела живлення Uдж і напруга двигуна подавання електрода Uпод.
Рисунок 1.10 - Зв'язна система
СКЛАДНІ СИСТЕМИ — це узагальнююча назва систем:
- які неможливо описати коректно математично
- які містять велику кількість елементів, пов'язаних між собою невідомим чином
- в яких невідома природа явищ, що відбуваються.
Прикладами таких систем є людський мозок, велике промислове підприємство.
СИСТЕМИ СТАБІЛІЗАЦІЇ— це системи, які призначені для автоматичного підтримання з заданою точністю постійного значення регульованої величини Xр.
В системі стабілізації задавальна дія Xз(t) є постійною величиною. Такі САР є найпростішими і набули найбільшого поширення в зварюванні, перш за все, для стабілізації напруги, струму або потужності зварювальних джерел живлення, швидкостей подавання присаджувального дроту, пересування зварювального пальника або виробу, режимів термообробки, положення зварювального пальника відносно зварюваного стику, провару при дуговому та електронно-променевому зварюванні. Стабілізація параметрів зварювального режиму та перерізу зварного шва в багатьох випадках дозволяє задовільно забезпечити потрібні експлуатаційні характеристики зварних з'єднань. Системи стабілізації можуть бути побудовані на принципі регулювання за відхиленням, за збуренням або на основі комбінації цих принципів.
СИСТЕМИ ПРОГРАМНОГО КЕРУВАННЯ(СПК) — це системи, які призначені для автоматичної зміни з заданою точністю регульованого параметру Y(t) за наперед заданим законом в функції часу або координат. В таких системах можна виділити дві основні частини: програмний пристрій ПП, що формує сигнал, та систему відтворення СВ, основним призначенням якої є забезпечення за допомогою керуючого пристрою КП заданої в ПП зміни вихідної координати об’єкту керування ОК (рис.1.11). В окремих випадках можлива корекція програми залежно від поточного стану керованої величини.
Рисунок 1.11 - Система програмного керування
Прикладом завдання програми в явній формі може бути зварювання неповоротних стиків труб. Такі з’єднання потребують програмування струму зварювання в залежності від просторового положення пальника таким чином, щоб глибина провару і ширина шву залишались незмінними. Параметричне завдання програми в зварюванні використовується значно частіше. Так при програмуванні режиму електронно-променевого зварювання задається синхронна і синфазна зміна більш ніж 10 параметрів для різних автономних і зв’язаних систем відтворення. СПК широко застосовуються в зварювальній техніці, перш за все, зважаючи на специфіку зварювального виробництва - необхідність використання універсального обладнання при виготовленні великої номенклатури різноманітних виробів. СПК, забезпечуючи можливість швидкого переналагоджування зварювального процесу при переході від одного типорозміру до іншого шляхом простої заміни програми, найбільш повно відповідають вимогам індивідуального та дрібносерійного виробництв, в умовах яких виготовляється більшість загального обсягу зварних конструкцій.
Об'єктами програмного керування в зварюванні можуть бути: послідовність в функції часу основних операцій зварювального циклу при різних способах зварювання, подавання присаджувального матеріалу при зварюванні плавленням, переміщення джерела нагрівання, зміна зварювального струму при контактному зварюванні, переміщення заготівок, що зварюються.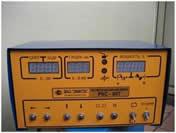
Операції збудження дуги та заварки кратера програмуються шляхом узгоджених змін швидкості подавання електроду і моментів вмикання та вимикання джерела живлення. Раціональним застосуванням СПК є також переміщення наплавляючого інструменту за трьома просторовими координатами і його поворот навкруги кожної вісі згідно профілю поверхні, що наплавляється. В деяких випадках необхідність програмування зварювального режиму викликається особливостями прийнятої технології зварювання. Наприклад, при зварюванні кільцевого неповороткого стику — нестаціонарністю температурного поля у виробі та розгалуженням теплового потоку дуги на основний, який рухається разом з дугою, та додатковий, що переміщується назустріч дузі. В цьому випадку корегування теплового режиму досягається шляхом програмного керування швидкості подавання присаджувального дроту і зварювального струму в залежності від положення ділянки стику, що зварюється. Останнє технічне рішення також є прикладом параметричного завдання програми.
СЛІДКУЮЧІ СИСТЕМИ — це системи, які призначені для автоматичної зміни з заданою точністю Y(t) у відповідності з наперед невідомою функцією часу, що визначається задавальною дією X(t).
За характером дії слідкуючи системи подібні до СПК, але відрізняються від них, перш за все відсутністю програматора, оскільки закон зміни X(t) наперед не відомий, формується в процесі роботи системи і визначається умовами, які існують за межами системи. Слідкуючи системи в зварюванні застосовують, перш за все, для автоматичного ведення електрода по стику зварюваних кромок при дуговому зварюванні.
ЕКСТРЕМАЛЬНІ СИСТЕМИ — це системи, в яких за допомогою безпосереднього виміру деякого показника якості роботи об’єкту і вироблення відповідної керуючої дії автоматично визначається і підтримується режим роботи, що характеризується максимально (мінімально) можливим значенням показника якості.
ЛІНІЙНІ СИСТЕМИ — це системи, властивості яких не залежать від величини вхідних дій.
Для лінійних систем справедливий принцип суперпозиції. Тобто якщо керована величина системи автоматичного керування Y1=F(X1) є функцією задавальної дії X1, а керована величина системи автоматичного керування Y2=F(X2) є функцією задавальної дії X2, то для задавальної дії X1+X2 керована величина Y=F(X1 +X2) набере значення Y1+Y2. Це означає, що властивості системи керування не залежать від зовнішніх дій на систему. В обмеженому діапазоні змін вхідної величини існує велика кількість елементів, для яких зазначенні умови виконуються (рис. 1.12).
Рисунок 1.12 - Резистор як приклад лінійного елемента САК
НЕЛІНІЙНІ СИСТЕМИ— це системи, властивості яких змінюються залежно від зовнішніх дій і для них не виконується принцип суперпозиції. Для більшості процесів зварювання застосовувати лінійні моделі навіть у малому інтервалі змін вхідних сигналів треба з обережністю (рис.1.13).
Рисунок 1.13 - Вольт-амперна характеристика дуги, як приклад нелінійного опору.
СТАЦІОНАРНІ СИСТЕМИ — це системи які не змінюють свої властивості з часом.
НЕСТАЦІОНАРНІ СИСТЕМИ (інша назва — зі змінними коефіцієнтами) — це системи, що змінюють свої властивості з плином часу.
Прикладом такої системи з галузі зварювання може служити електрошлакове зварювання. Вигоряння і перехід у гарнісаж деяких елементів флюсу під час зварювання призводить до суттєвих змін властивостей шлакової ванни, яка є джерелом нагріву при ЕШЗ. Для нестаціонарних лінійних об’єктів принцип суперпозиції є справедливим. Однак з інженерної точки зору нестаціонарність призводить до значних відмінностей, оскільки стає непридатним широко вживаний математичний апарат — перетворення Лапласа. В зварюванні нестаціонарні лінійні системи відповідають неквазістаціонарним процесам.
НЕПЕРЕРВНІ СИСТЕМИ — це системи, в яких сигнал передається неперервним в часі і є неперервним за рівнем. Часто такі системи називають також аналоговими
ДИСКРЕТНІ СИСТЕМИ — це системи, в яких передається та перетворюється сигнал, квантований за рівнем або/і за часом. Такі системи мають елемент, який при безперервній зміні сигналу на вході передає його далі переривчасто - дискретно.
РЕЛЕЙНІ СИСТЕМИ — це системи, до складу яких входить релейний елемент, завдяки якому регулююча дія Y(t) на виході регулятора в залежності від вхідного сигналу може приймати два (двохпозиційні системи) або три (трипозиційні системи) постійних значення:
Ymax - Ymin
або
Ymax - 0 - Ymin.
Релейні системи конструктивно прості, мають максимальну швидкодію, дозволяють легко отримувати великі коефіцієнти підсилення. Але вони мають знижену точність регулювання і схильні до автоколивань.
ІМПУЛЬСНІ СИСТЕМИ— це системи, в яких сигнал квантується за часом (сигнал дискретний за часом) і керуюча дія видається у визначені моменти часу і відсутня в проміжках між ними.
В системах тільки один з параметрів імпульсу — амплітуда А, шпаруватість σ (відношення періоду Т до тривалості імпульсу tі) або частота f (період T) їх повторення — є функцією вхідного сигналу, а інші два - залишаються постійними. Відповідно розрізняють амплітудно-імпульсний (A=var, f=const, σ =const), широтно-імпульсний (A=const, f=const, σ =var) і частотно-імпульсний (A=const, f=var, σ =const) методи регулювання (рис.1.14).
Рисунок 1.14 - Різновиди імпульсних систем
ЦИФРОВІ СИСТЕМИ — це системи, в яких керуюча дія - сигнал, квантований за часом і за амплітудою, відображається у вигляді коду.
Цифрові системи використовують, перш за все, для програмного керування зварювальними циклами, положенням та переміщеннями робочих органів зварювальних установок, зміни електричних параметрів режимів, тощо. Системи із складною програмою реалізації математичних та логічних операцій будуються на базі використання обчислювальних пристроїв та ЕОМ. В багатьох випадках дискретне керування застосовують спеціально для підвищення перешкодозахищенності систем. Для переходу від неперервних систем до дискретних та навпаки застосовують аналого-цифрові (АЦП) та цифро-аналогові (ЦАП) перетворювачі (рис.1.15).
Рисунок 1.15 - Функціональна схема цифрової САК
РОЗІМКНУТІ СИСТЕМИ — системи, в яких потрібний закон зміни керованої величини забезпечується шляхом безпосереднього перетворення завдання в керуючу дію без урахування значення, яке досягається в результаті керування.
В таких системах завдання X(t) не співставляються з керованою величиною Y(t) і відхилення дійсного режиму роботи об'єкту від заданого не впливають на керуючу дію і самою системою не усуваються. До розімкнених систем відносяться найпростіші системи автоматичного захисту обладнання від аварій при виникненні нештатних ситуацій, системи блокування — для захисту обладнання від помилкових дій обслуговуючого персоналу, включаючи відсутність належних умов (охолоджуючої води, електродного дроту, тощо) для роботи обладнання, а також для включення резервних пристроїв при виході з ладу основних. Розімкненими є також системи автоматичного контролю, які виконують виміри, сигналізацію та реєстрацію вихідних параметрів об'єкту (напруги і струму дуги, зусилля стискання електродів машин контактного зварювання та ін. ). Часто проектуються як розімкнуті системи програмного керування (СПК). Основним недоліком розімкнених СПК є низька точність при дії на об'єкт різного роду збурень, оскільки жорстке програмування виключає можливість урахування впливу збурень на Y. Якість керування в розімкнених системах суттєво поліпшується при доповненні їх компенсуючими зв'язками по основним збуренням - у відповідності з принципом регулювання за збуренням.
ЗАМКНУТІ СИСТЕМИ — це системи автоматичного керування, в яких керуюча дія виробляється з урахуванням значення регульованої величини, яке досягається в результаті керування.
Таким чином, замкнуті системи використовують принцип керування за відхиленням. Інформація про фактичне значення регульованої величини перетворюється пристроєм зворотного зв'язку в сигнал головного зворотного зв'язку, який надходить на вхід системи, де порівнюється в елементі порівняння (суматорі) з завданням. При відхиленні з'являється сигнал розузгодження, який використовується для вироблення регулюючої дії, що спрямована на зменшення розузгодження.
ТЕОРЕТИЧНІ ОСНОВИ АВТОМАТИЧНОГО КЕРУВАННЯ
ТИПОВА ФУНКЦІОНАЛЬНА СХЕМА САР ТА ЇЇ ОСНОВНІ СКЛАДОВІ ЧАСТИНИ
Типова функціональна схема САР, що реалізує принцип регулювання за відхиленням (рис.1.16,а) відображає взаємодію об'єкту регулювання ОР і регулятора Р, поданого у розгорнутому вигляді, пристрої та елементи якого за їх призначенням класифікують таким чином:
- ЗП - задавальний пристрій який служить для перетворення задавальної дії в сигнал, придатний для подальшої роботи системи.
- Р – регулятор, пристрій, який служить для реалізації необхідного закону керування
- П – підсилювач, узгоджує за рівнем і потужністю вихідний сигнал з обчислювача з вхідним сигналом виконавчого пристрою
- ВП – виконавчий пристрій, що безпосередньо діє на об’єкт автоматичного керування
- ОР – об’єкт регулювання, технологічний процес
- Д – датчик, елемент системи, що перетворює інформацію про фізичну величину в сигнал, зручний для використання і перетворення в системах автоматичного контролю та керування.
Реальні системи автоматичного регулювання можуть містити досить складні елементи, які в свою чергу, можуть розглядатись як системи автоматичного керування. На рис. 1.16,б наведена така система керування за відхиленням, що містить виконавчий пристрій, який є окремою системою автоматичного регулювання і працює за збуренням і відхиленням одночасно.
Рис. 1.16 Типова функціональна схема САК
Датчики САР
ДАТЧИК - елемент системи, що перетворює інформацію про фізичну величину в сигнал, зручний для використання і перетворення в системах автоматичного контролю та керування
Функціонально необхідним і обов'язковим є сприймаючий елемент датчика, який контролює поточне значення регульованої величини і повинен мати на виході величину тієї фізичної природи, яка прийнята в даній системі для вироблення регулюючої дії. Частіше за все це різні електричні параметри: струм, напруга, фаза та ін. Якщо елементом Д контролюється неелектрична величина, то її необхідно перетворити, як правило, в адекватний електричний сигнал.
При вирішенні задач автоматизації ТПЗ сигнал, що видається датчиком, як правило недостатній за потужністю для безпосереднього приведення в дію регулюючих органів об'єктів. Вихідна потужність датчика в багатьох випадках не перевищує величин порядку (10...4) Вт, тоді як потужність виконуючих пристроїв вимірюється кіловатами. Це вимагає необхідного підсилення вихідного сигналу датчика.
Підсилювачі
ПІДСИЛЮВАЧІ - пристрої, які служать для кількісного перетворення за величиною або потужністю сигналів керування.
Якщо підсилення здійснюється тільки за величиною сигналу (трансформатор-підсилювач напруги, редуктор-підсилювач кутової швидкості та інші подібні), то для роботи такого підсилювача не потрібне споживання зовнішньої енергії. При цьому потужність сигналу на виході підсилювача виявляється меншою, ніж на вході внаслідок втрат її в самому підсилювачі.
В САР зварювальними процесами підсилювачі використовуються переважно для підсилення сигналів за потужністю з тим, щоб вона виявилась достатньою для керування виконуючими пристроями. Тому такі підсилювачі вимагають для своєї роботи споживання зовнішньої енергії. Якщо сигнал, який поступає на вхід підсилювача і сигнал, потрібний для керування виконуючим пристроєм відрізняються за фізичною природою, в функції підсилювача входить також і перетворення сигналів.
Таким чином, якщо потужність датчика недостатня для безпосереднього керування об'єктом, вихідний сигнал датчика підсилюється і перетворюється пристроєм в керуючу дію з використанням енергії додаткового зовнішнього джерела.
Регулятори з підсилювально-перетворюючими пристроями, що діють на регулюючий орган об'єкту ОР через підсилювач потужності та виконуючий пристрій і які живляться від зовнішнього джерела живлення, називають регуляторами непрямої дії.
Регулятори в яких сигнал з датчика достатній за потужністю для безпосередньої дії на об’єкт регулювання називають регуляторами прямої дії.
Виконавчий пристрій
ВИКОНАВЧИЙ ПРИСТРІЙ - пристрій, що безпосередньо впливає на об’єкт керування (регулювання), змінюючи його стан у відповідності до сигналів, які надходять з обчислювача.
Якщо в системі керування для зміни стану об’єкту необхідно докласти механічних зусиль, то як виконавчий пристрій використовують електричні, гідравлічні, пневматичні або комбіновані двигуни. Такі двигуни класифікують також за видом руху (обертове, лінійне), характером руху (неперервне, дискретне), за потужністю, швидкодією, точністю і тому подібне. Такі двигуни називають сервомоторами.
СЕРВОМОТОРИ - це окремий вид двигуна, який характеризується спеціальним режимом роботи. Якщо звичайний двигун працює в усталеному режимі, коли вмикання, вимикання, зміна швидкості виконуються нечасто. У сервомоторів автоматичне регулювання здійснюється безперервно, вимагаючи постійної зміни швидкості як за величиною, так і за знаком.
Найбільше надійними є гідравлічні сервомотори, які мають ресурс безвідмовної роботи 15000…20000 годин. Найменше надійними є електродвигуни постійного струму 1000…2000 годин. Однак, саме електродвигуни (з відповідними керуючими схемами) найшли найбільше широке застосування в зварювальному виробництві завдяки:
- широкому діапазону регулювання кутових швидкостей обертання;
- зручності керування та комутації;
- малим габаритам та масі, особливо в діапазоні потужностей до 1кВт.
Як сервомотори в зварювальних установках використовують в значній мірі пристрої загальнопромислового призначення.
Регулятор
РЕГУЛЯТОР - пристрій, що служить для реалізації необхідного закону регулювання. У відповідності до математичного виду цього закону регулятор може бути
- пропорційним;
- пропорційно-інтегральним;
- пропорційно-інтегрально-диференціальним.
Зміною параметрів настроювання регулятор може бути пристосований для рішення різних задач керування. Складніші з них вимагають, як правило, застосування систем, які включають декілька регуляторів.
Кожна задача автоматичного керування зварювальним циклом як окремий випадок загальної проблеми обробки інформації може бути представлена сукупністю окремих операцій, які виконуються у визначеній послідовності, тобто за програмою. В сучасній техніці найбільш поширеним і універсальним пристроєм, який виконує заданий програмний процес вирішення задачі, є мікропроцесор. На основі мікропроцесорів, доповнених пам’яттю, зовнішніми пристроями і набором засобів зв'язку створені мікро-ЕОМ, які завдяки малим габаритам, масі, потужності, що споживається і високій надійності стали основою вільно-програмованих САК. Головною особливістю таких систем є модульність апаратних засобів, які в них використовуються, що дозволяє створювати за єдиною схемою САК різними технологічними процесами зварювання, незалежно від типів технологічного обладнання, яке при виконанні цих процесів використовується.
Найбільш типовим для сучасного зварювального виробництва є використання систем, в яких основний програмно-логічний цикл керування виконується СПК, в тому числі вільно-програмованими системами на базі мікро-ЕОМ, з широким застосуванням локальних САК (регуляторів) визначальних параметрів процесу. За родом енергії, що використовується, такої САК поділяють на електромеханічні, електронні, пневматичні, гідравлічні, а також змішані - електропневматичні, електрогідравлічні, тощо. Незважаючи на суттєві відмінності таких систем як за функціональними можливостями, так і за конструктивною реалізацією, все різноманіття елементів та пристроїв, що входять в різні САК, за функціональним призначенням може бути зведено до декількох основних типів. Це, в свою чергу, дозволяє роботу любої САК відобразити узагальненою функціональною схемою, в якій кожна конструктивно відокремлена частина системи, що виконує визначені функції, відображається окремим блоком. Зв'язки між цими функціональними блоками (внутрішні дії) позначаються лініями зі стрілками, які указують напрямок дії.
Принципи будови автоматичних систем Приклади автоматичних систем регулювання, контролю та захисту
Принципи побудови автоматичних систем
У техніці використовуються три фундаментальних принципи:
3) Принцип зворотного зв'язку (керування за відхиленням).
Принцип розімкненого керування полягає в тому, що алгоритм керування ґрунтується тільки на заданому алгоритмі функціонування і не контролюється збуреннями чи вихідними координатами. Структурна схема САР з принципом розімкненого керування наведена на рис.1.1
Рис.1.1
ЗП – задавальний пристрій; Р – регулятор; ОР – об'єкт регулювання; g – задавальний вектор станів пристрою; у – вектор станів регулятора; f – збурення;x – вектор станів об'єкта регулювання (вихідна величина).
У такій системі контроль за фактичним станом об'єкта регулювання не здійснюється, тому що близькість до бажаної поведінки системи забезпечується тільки точністю всіх елементів системи і відповідним вибором задавального вектора станів. Прикладом такої системи є параметричний стабілізатор напруги на стабілітроні. По розімкненому принципу побудовані пристрої пуску, лінійні підсилювачі, перетворювачі та ін.
Для компенсації відхилення x, що відбувається за рахунок появи збурень застосовують принцип компенсації та принцип зворотного зв'язку.
Принцип компенсації полягає в перетворенні збурення у величину того ж характеру, що і задавальний вплив, і зміні вектора регулятора таким чином, щоби здійснювалася повна компенсація збурення. Для цього вводиться канал компенсації КК.
Структурна схема САР з принципом компенсації наведена на рис.1.2.
Рис.1.2
Перевагою принципу компенсації є можливість досягти інваріантості по збуренню. Недоліком є те, що відхилення вхідної величини від заданого значення може бути викликане впливом інших збурень.
Принцип компенсації використовується в системах стабілізації змінних стану об’єкта регулювання (струму, напруги, сили звуку, положення в просторі, тощо) в умовах збурень (зміна струму навантаження, напруга мережі, тощо).
У статичному режимі для систем стабілізації існують наступні типи залежностей вихідної величини x(t) від величини збурення f (рис.1.3):
1 – перекомпенсація;
2 – інваріантність – властивість системи, в якій збурення не впливає на вихідну величину;
3 – недокомпенсація;
4 – нелінійна залежність.
Рис.1.3
Принцип керування по відхиленню полягає в тому, що вихідна величина вимірюється, і порівнюється з задавальним впливом. У результаті виділяється деяке відхилення (сигнал неузгодженості , рис.1.4), що перетворюється у вектор регулювання y, який впливає на ОР таким чином, щоби зменшити зміну х.
Рис.1.4
У системі автоматичного регулювання для реалізації керування по відхиленню вводять зворотний зв’язок на відміну від принципу компенсації, в якому немає зворотного зв’язку, і вихідна величина не надходить на вхід схеми.
Переваги принципу зворотного зв’язку:
1) відхилення х зменшується незалежно від того, якими факторами воно викликане;
2) менша чутливість до зміни параметрів елементів схеми в порівнянні з розімкненими системами;
3) принцип можна застосовувати до об'єктів, характеристики яких невідомі – бажано знати характеристики об’єкту, але не обов’язкове детальне і точне знання всіх характеристик, більш принциповою є умова можливості керування, тобто керованості об’єкту керування;
4) технічно легше реалізовується в порівнянні з розімкненими системами, де необхідний точний попередній розрахунок всіх параметрів, характеристик та сигналів, їх узгодження між собою, а також підлаштування параметрів в процесі роботи.
Недоліки:
1) у простих одноконтурних системах не можна досягти повної інваріантності;
2) для систем із зворотними зв’язками характерна проблема стійкості.
Застосування комбінованого регулювання по збуренню та відхиленню підвищує ефективність регулювання. Комбіновані регулятори поєднують переваги обох принципів – швидкість реакції на зміну збурення і точне регулювання незалежно від причини, що викликала відхилення.
Лекція 20. Датчики систем автоматики. Датчики слідкуючих систем
Датчики та перетворення вимірюваної величини у процесі вимірювань
Якщо проаналізувати відомі процеси вимірювань, то переважно кількісне значення вимірюваної величини отримується тільки після того, як тим чи іншим способом ми її видозмінимо.
Як приклад розглянемо процес визначення маси тіла за допомогою звичайних рівноплечих ваг. Під дією земного тяжіння створюються сили. Маса тіла разом з цими силами тисне на одну чашку, а маса гир – на іншу. Підбираючи гирі, ми досягаємо рівноваги вимірюваної маси та гир, приймаючи, що сила земного тяжіння між чашками залишається однією і тією ж. Отже для вимірювання маси нам довелося перетворювати маси тіла та гир в сили, а для порівняння сил між собою перетворювати їх дію в механічне переміщення важелів ваг.
Інший приклад – вимірювання тиску газу за допомогою трубчатого манометра. Металічна трубка манометра, яка зігнута дугою, одним кінцем з’єднується з резервуаром, у якому необхідно виміряти тиск газу. Інший кінець трубки запаяний. Під дією тиску газу трубка розгинається і тим більше, чим більший в ній тиск. Вільний кінець трубки переміщується у просторі. Так відбувається перший етап перетворення. Це переміщення кінця за допомогою системи важелів та зубчатих кілець перетворюється в обертання вісі (другий етап перетворення). На вісі закріплена стрілка, кінець якої переміщується над шкалою з поділками. Цей третій етап перетворення і дає змогу отримати кількісне значення тиску, що вимірюється.
Наведені приклади показують, що навіть прості вимірювання проводяться шляхом перетворення вимірюваної величини. Для таких перетворень використовуються різноманітні первинні перетворювачі.
В автоматичних пристроях широко застосовують електричну енергію, яка володіє рядом переваг у порівнянні з іншими видами енергії. Серед переваг можна зазначити: простота передачі на значні віддалі, можливість акумулювання тощо. Однак величини, які характеризують більшість процесів на транспорті – неелектричні: швидкість, переміщення, температура, тиск тощо. У зв’язку з цим часто виникає потреба у перетворенні різноманітних неелектричних величин в електричні сигнали, які змінюються відповідно до змін неелектричних вимірюваних величин. Елементи, які призначені виконувати вказані перетворення називають датчиками (чи перетворювачами).
Електричні датчики, які перетворюють неелектричні вхідні величини в електрорушійну силу чи напругу, називають генераторними (активними) датчиками. Ці датчики не потребують зовнішнього джерела живлення. Датчики, в яких вимірювання неелектричної величини супроводжується відповідною зміною того чи іншого електричного параметра (індуктивності, ємності, опору), називають параметричними (пасивними). Параметричні датчики отримують енергію від допоміжного джерела живлення.
До датчиків ставляться наступні вимоги: неперервність та лінійність статичної характеристики, висока чутливість, низька інерційність, висока надійність, мінімальні вартість, габаритні розміри та маса.
Галузі застосування датчиків на залізничному транспорті.
На залізниці датчики застосовують у системах:
– напівавтоматичного та автоматичного блокування (ПАБ, АБ) для контролю зайнятості перегону та блок-дільниць;
– автоматичної локомотивної сигналізації (АЛС), автоматичного регулювання швидкості та автоматичного управління гальмами (САУТ) з метою отримання інформації про фактичну швидкість та місце знаходження поїздів;
– переєзній сигналізації (АПС) та огороджувальних пристроях для сигналізації про наближення поїзда, контролю швидкості наближення та швидкості руху;
– гіркової автоматизації (ГАЦ, АРС) для визначення швидкостей та прискорень відчепів з метою управління засобами їх гальмування, а також для контролю вільного стану стрілочних ділянок і вимірювання ваги відчепів;
– виявлення перегрітих букс (ПОНАБ, ДИСК), наявності повзунів на колесах в поїздах з метою виявлення порушень нормальних умов експлуатації рухомого складу та реєстрації кількості осей, які проходять через контрольну точку;
– у вимірювальних вагон-лабораторіях.
Розглянемо найпоширеніші типи датчиків.
Індуктивні датчики знаходять широке застосування в машинобудуванні, харчовій, текстильній та інших галузях. Вони найбільш ефективно використовуються в якості кінцевих вимикачів в автоматичних лініях і верстатах, так як індуктивні датчики спрацьовують тільки на метали і не чутливі до решти матеріалів.
Індуктивний датчик – це перш за все безконтактний вимикач, який не містить рухомих деталей і практично не піддається впливу навколишнього середовища. Основне призначення – безконтактний контроль положення предметів, виготовлених з електропровідних або магнітопровідних матеріалів.
Від датчиків, заснованих на інших принципах дії, але створених для тих же цілей, індуктивні датчики мають ряд значимих відмінностей і переваг, в числі яких висока довговічність, завдяки відсутності зіткнень і технічних впливів, чутливість тільки до металу і можливість різних варіантів виконання. Такі датчики не реагують на рідину, мастило, дотик рук, що дуже зручно і практично у виробничому процесі.
Індуктивні датчики влаштовані простіше і коштують менше, ніж ємнісні і ультразвукові. Конструкція датчиків забезпечує захист від короткого замикання і можливість функціонування в діапазоні температур від -25 до + 70 ° С.
До інших переваг таких датчиків відносять: простоту і міцність конструкції, відсутність ковзних контактів; можливість підключення до джерел промислової частоти; відносно велику вихідну потужність (до десятків Ватт); значну чутливість.
Переваги
- Ні механічного зносу, відсутні відмови, пов’язані зі станом контактів
- Відсутня брязкіт контактів і помилкові спрацьовування
- Висока частота перемикань до 3000 Hz
- Стійкий до механічних впливів
Недоліки – порівняно мала чутливість, залежність індуктивного опору від частоти живлячої напруги, значне зворотний вплив датчика на вимірювану величину (за рахунок тяжіння якоря до сердечника).
Контактні датчики – це найпростіший вид резисторних датчиків, які перетворять переміщення первинного елемента в стрибкоподібне зміна опору електричного кола. За допомогою контактних датчиків вимірюють і контролюють зусилля, переміщення, температуру, розміри об’єктів, контролюють їх форму і т. д. До контактних датчиків належать колійні та кінцеві вимикачі, контактні термометри і так звані електродні датчики, використовувані в основному для вимірювання граничних рівнів електропровідних рідин.
Контактні датчики можуть працювати як на постійному, так і на змінному струмі. Залежно від меж вимірювання контактні датчики можуть бути одно граничними. Останні використовують для вимірювання величин, що змінюються в значних межах, при цьому частини резистора R, включеного в електричний ланцюг, послідовно закорочуються.
Недолік контактних датчиків – складність здійснення безперервного контролю і обмежений термін служби контактної системи. Але завдяки граничній простоті цих датчиків їх широко застосовують в системах автоматики.
Ємнісні датчики – принцип дії заснований на залежності електричної ємності конденсатора від розмірів, взаємного розташування його обкладок і від діелектричної проникності середовища між ними.
Ємнісні датчики, також як і індуктивні, харчуються змінною напругою (зазвичай підвищеної частоти – до десятків мегагерц ). В якості вимірювальних схем зазвичай застосовують мостові схеми і схеми з використанням резонансних контурів. В останньому випадку, як правило, використовують залежність частоти коливань генератора від ємності резонансного контуру, тобто датчик має частотний вихід.
Переваги ємнісних датчиків – простота, висока чутливість і мала інерційність. Недоліки – вплив зовнішніх електричних полів, відносна складність вимірювальних пристроїв.
Ємнісні датчики застосовують для вимірювання кутових переміщень, дуже малих лінійних переміщень, вібрацій, швидкості руху і т. д., а також для відтворення заданих функцій ( гармонійних, пилкоподібних, прямокутних і т. п.).
Потенциометрический датчик являє собою змінний резистор, до якого прикладено напругу живлення, його вхідний величиною є лінійне або кутове переміщення токоз’ємного контакту, а вихідний величиною – напруга, що знімається з цього контакту, що змінюється за величиною при зміні його положення.
Потенціометричні датчики призначені для перетворення лінійних або кутових переміщень в електричний сигнал, а також для відтворення найпростіших функціональних залежності в автоматичних і автоматичних пристроях безперервного типу.
Переваги потенціометричних датчиків:
- простота конструкції;
- малі габарити і вага;
- висока ступінь лінійності статичних характеристик;
- стабільність характеристик;
- можливість роботи на змінному та постійному струмі.
Недоліки потенціометричних датчиків:
- наявність ковзного контакту , який може стати причиною відмов через окислення контактної доріжки , перетирання витків або відгинання повзунка;
- похибка в роботі за рахунок навантаження;
- порівняно невеликий коефіцієнт перетворення;
- високий поріг чутливості;
- наявність шумів;
- схильність електроерозії під дією імпульсних розрядів.
Термопари є самими високотемпературними контактними датчиками температури. Принцип дії термопар заснований на термоелектричному ефекті, відкритим німецьким фізиком Томасом Зєєбеком в 1821 р. Якщо з’єднати два різнорідних провідника і підтримувати місця з’єднання при різних температурах, то між кінцями виникне електрорушійна сила (термо-ЕРС ). Такі з’єднання називаються термопарами. Величина виникає термоЕРС залежить від матеріалу провідників і різниці температур між спаями. У невеликому діапазоні температур термоЕРС пропорційна різниці температур.
Головним достоїнством термопар є великий температурний діапазон вимірювання від -200 ° С до 2500 ° С, а також простота і міцність конструкції , і невисока ціна. Основні недоліки термопар – точність вимірювання від 1 ° С, необхідність компенсації температури холодного спаю (у сучасних приладах вводиться автоматична поправка до виміряної ЕРС), нелінійна залежність напруги на виході термопари від температури.
Цифрові напівпровідникові датчики температури останнім часом активно просуваються на агропромисловому ринку. Чутливі елементи для них виробляють світові лідери в галузі мікроелектроніки. Чутливий елемент являє собою інтегральну мікросхему, що містить в собі чутливий елемент і перетворювач в цифровий сигнал.
Основні переваги цих датчиків: зручна схема підключення (не вимагає прокладки індивідуальної кабельної лінії безпосередньо до датчика, датчики підключаються на одну загальну лінію), цифровий сигнал, що дозволяє уникнути застосування різних перетворювачів для побудови вимірювальної ланцюга, і невисока ціна. Недоліками цих датчиків є вкрай слабка завадостійкість (датчики можуть серйозно брехати, якщо поруч проходить силова лінія або працюють електродвигуни) і невисока точність (всього лише 0,5 ° С). Обмежений робочий діапазон цих датчиків – до 125 ° С – не дозволяє застосовувати їх у різних теплообмінних установках, де температура теплоносія може досягати 130-150 ° С.
Лекція 21. Датчики Холу та магнітних величин
Датчики Холу
ДаліЕфе́кт Хо́лла — явище, при якому виникає поперечна різниця потенціалів під час розміщення провідника з постійним струмом у магнітному полі. Відкритий Едвіном Холлом у 1879 році в тонких пластинах золота.
Властивості
У найпростішому розгляді ефект Холла має такий вигляд. Нехай через металевий брусок у слабкому магнітному полі
протікає електричний струм під дією напруженості
. Магнітне поле буде відхиляти носії заряду (для визначеності електрони) від їхнього руху вздовж або проти електричного поля до однієї з граней бруса.
Таким чином, сила Лоренца призведе до накопичення від'ємного заряду біля однієї грані бруса та додатного – біля протилежної грані. Накопичення заряду продовжуватиметься доти, поки електричне поле зарядів
, яке виникло під дією магнітного поля, не врівноважить магнітну складову сили Лоренца:
Коефіцієнт
пропорційності між
та
називається коефіцієнтом Холла. У такому наближенні знак коефіцієнта Холла залежить від знака носіїв заряду, що дозволяє визначати їхній тип для великого числа металів. Для деяких металів (наприклад, таких як свинець, цинк, залізо, кобальт, вольфрам), у сильних полях спостерігається додатний знак
, що пояснюється в напівкласичній і квантовій теоріях твердого тіла.
Застосування
Сенсор Холла, що використовується для вимірювання сили струму у провіднику. На відміну від трансформатора струму, вимірює також і постійний струм.
Ефект Холла, у деяких випадках, дозволяє визначити тип носіїв заряду (електронний або дірковий) у металі або напівпровіднику, що робить його придатним для дослідження властивостей напівпровідників. На основі ефекту Холла функціонують сенсори Холла: прилади, що вимірюють напруженість магнітного поля. Сенсори Холла набули поширення у безколекторних, або вентильних, електродвигунах (сервомоторах). Сенсори закріплюються безпосередньо на статорі двигуна та виступають в ролі датчика положення ротора, що реалізує зворотний зв'язок з положення ротора. На основі ефекту Холла працюють деякі види іонних реактивних двигунів.
Датчик Холла призначається для того, щоб вимірювати швидкість переміщення для індикації параметрів виконавчих механізмів пристроями системи автоматичного управління. Інформація, яка надходить від датчика, необхідна, щоб формувати керуючі сигнали в системі регулювання і стабілізувати параметри переміщення вузлів об'єкта автоматизації.
Основу складає так званий елемент Холла, який з'єднаний з електричною схемою. Датчик Холла - це мікросхема, на виході якої формується необхідний інформаційний сигнал. Основа принципу роботи пристрою - це магнітне поле, яке фіксується. Для того щоб виміряти швидкість переміщення, датчик Холла закріплюють на нерухомих елементах конструкції, а до рухається частини прикріплюють магніти. Є й більш простий спосіб: рухливі контакти і елементи просто намагничивают. При цьому ніяких змін у конструкцію не вноситься. Для того щоб виміряти швидкість обертання, застосовують пару постійних магнітів і той же самий датчик Холла. Принцип роботи в такому випадку простий: між цими двома полюсами переміщається у вільному стані пластинка, яка екранує магнітне поле. Кожен оборот - це формування електричного імпульсу в електронний тахометр. Для того щоб збільшити точність, використовують просто більшу кількість магнітів.
Датчик Холла зобов'язаний своєю появою знаменитому американському вченому, який і дав приладу своє ім'я. Едвін Холл зробив в 1879 році дуже важливе відкриття цього гальванічного і магнітного явища.
Практичну цінність цього винаходу складно переоцінити. Сам ефект полягає в тому, що, якщо протікає струм вздовж якогось провідника, на який здійснюється вплив поперечним магнітним полем, то виникає електричне поле. Таке явища називається ЕРС (електрорушійної силою) Холла. Найперші прилади на основі цього ефекту були громіздкі і не особливо ефективні. Розвиток електроніки, зокрема мікропроцесорної техніки, вдихнуло нове життя в розвиток таких пристроїв. Мікросхеми стали використовуватися в такому пристрої, як датчик Холла. Більше того, існують мініатюрні прилади. Вони можуть бути лінійними: для зчитування інформації про струм, про вібрації, про положення і так далі. І вони можуть бути логічними: датчики частоти обертання, наближення, імпульсів. На даний момент розроблені високоефективні цифрові пристрої на основі ефекту Холла.
Датчик Холла в першу чергу призначається для автоматизації ліній в транспортних і поточних системах. Також він використовується для контролю положень вузлів в різних механізмах: положення і переміщення деталей від початкових і до кінцевих положень. Цей пристрій використовується і для вимірювання струмів, і як чутливий елемент у магнітного компаса. За допомогою такого приладу, як датчик Холла, можна вимірювати також і потужність, і швидкість, і відстань. У приводах дисководів у будь-якого ПК є ЕРС Холла.
Лекція 22. Датчики частоти обертання. Приклади використання на рухомому складі
Датчики частоти обертання. Тахометри
Як датчики частоти обертання в системах автоматики застосовують тахогенератори - малопотужні електричні машини постійного і змінного струму. Для перетворення частоти обертання електродвигунів в напругу застосовують тахометричні мости.
Тахогенератори постійного струму
Тахогенератори постійного струму в залежності від способу збудження виконують двох типів: магнітоелектричні (порушувані від постійних магнітів) і електромагнітні (порушувані від спеціальної обмотки) (рис. 22. 1 а, б).
Тахогенератори постійного струму
Тахогенератори постійного струму в залежності від способу збудження виконують двох типів: магнітоелектричні (порушувані від постійних магнітів) і електромагнітні (порушувані від спеціальної обмотки) (рис. 22. 1 а, б).
Напруга на виході тахогенератора при постійному потоці збудження
U вих = Е - IRя = Сеω - IRя
де Се = (Uя - IяRя) / ω - постійна машини, визначається з паспортних даних.
На холостому ходу (I = 0) напруга U вих = Е = Сеω. Отже, статична характеристика тахогенератора U вих = f (ω) при холостому ході лінійна, так як Се = const (пряма 1, рис. 22.1, в).
При навантаженні статична характеристика стає нелінійної (крива 2). змінюється її нахил, що є наслідком реакції якоря і падіння напруги в обмотці якоря тахогенератора. У реальних тахогенераторах виникає падіння напруги на щітках, що призводить до появи юні нечутливості (крива 3).
Для зменшення спотворення статичних характеристик тахогенераторів використовують при невеликих навантаженнях (Iн = 0,01 - 0,02 А). Струм в ланцюзі якоря I я = Е / (R я + Rн), а вихідна напруга U вих = Е - IRя = Сеω - IRя.
Тахогенератори постійного струму широко застосовуються в автоматичних системах регулювання електроприводів як датчики частоти обертання. Їх переваги - мала інерційність висока точність, малі габарити і маса, а для магнітоелектричних тахогенераторів ще й відсутність джерела живлення. Недолік - наявність колектора зі щітками.
Для зменшення спотворення статичних характеристик тахогенераторів використовують при невеликих навантаженнях (Iн = 0,01 - 0,02 А). Струм в ланцюзі якоря I я = Е / (R я + Rн), а вихідна напруга U вих = Е - IRя = Сеω - IRя.
Тахогенератори постійного струму широко застосовуються в автоматичних системах регулювання електроприводів як датчики частоти обертання. Їх переваги - мала інерційність висока точність, малі габарити і маса, а для магнітоелектричних тахогенераторів ще й відсутність джерела живлення. Недолік - наявність колектора зі щітками.
Рисунок 22.2 - Зовнішіній вигляд тахомера
Тахогенератори змінного струму
Синхронні тахогенератори - однофазна синхронна машина з ротором у вигляді постійного магніту (рис. 22.3, а), У синхронних тахогенераторів зі зміною кутової швидкості разом з амплітудою змінюється і частота вихідної напруги. Статичні характеристики нелінійні. У динамічній щодо синхронні тахогенератори є безінерційними елементами.
Асинхронний тахогенератор - це двофазна асинхронна машина з порожнистий немагнітним ротором (рис. 22.3, б). На статорі асинхронного тахогенератора розміщуються дві зсунуті на 90 обмотки (збудження ОВ і генератора ОГ). Обмотка ОВ підключається до джерела змінного струму.
Синхронні тахогенератори - однофазна синхронна машина з ротором у вигляді постійного магніту (рис. 22.3, а), У синхронних тахогенераторів зі зміною кутової швидкості разом з амплітудою змінюється і частота вихідної напруги. Статичні характеристики нелінійні. У динамічній щодо синхронні тахогенератори є безінерційними елементами.
Асинхронний тахогенератор - це двофазна асинхронна машина з порожнистий немагнітним ротором (рис. 22.3, б). На статорі асинхронного тахогенератора розміщуються дві зсунуті на 90 обмотки (збудження ОВ і генератора ОГ). Обмотка ОВ підключається до джерела змінного струму.
РИсунок 22.2 - Тахомерічні генератори змінного струму: асинхронний, б - асинхронний
В обмотці OВ, що є вихідною, при обертанні ротора наводяться ЕРС трансформації і обертання. Під дією ЕРС обертання на виході тахогенератора виникає напруга U вих.
Статична характеристика асинхронного тахогенератора також нелінійна. При зміні обертання ротора фаза вихідної напруги змінюється на 180.
Статична характеристика асинхронного тахогенератора також нелінійна. При зміні обертання ротора фаза вихідної напруги змінюється на 180.
Асинхронні тахогенератори використовують як датчики кутової швидкості, частоти обертання і прискорень. В останньому випадку обмотка збудження асинхронного тахогенератора підключається до джерела постійного струму.
Переваги асинхронних тахогенераторів - надійність, мала інерційність. Недоліки - наявність на виході залишкової ЕРС при нерухомому роторі, відносно великі габарити.
Переваги асинхронних тахогенераторів - надійність, мала інерційність. Недоліки - наявність на виході залишкової ЕРС при нерухомому роторі, відносно великі габарити.
Енкодери - пристрої, призначені для перетворення кута повороту обертового об'єкта (вала) в електричні сигнали, що дозволяють визначити кут його повороту.
Енкодери підрозділяються на інкрементальні енкодери і абсолютні, які можуть досягати дуже високої точності.
Енкодери можуть бути як оптичні, резисторні, так і магнітні і можуть працювати через шинні інтерфейси або промислову мережу.
В абсолютних енкодерах (датчиках кутового положення) - однооборотний і багатооборотних - позиція закодована у вигляді штрихового коду і не втрачається при зникненні напруги. У тому випадку, якщо після зникнення напруги, позиція вала буде змінена, при повторному включенні системи енкодер відразу видасть інформацію про новому положенні вала і номер обороту (для багатооборотних енкодерів). В основі роботи енкодера лежить принцип безконтактного оптоелектронного зчитування інформації.
Принцип роботи інкрементального енкодера
Імпульсний (покроковий) енкодер відноситься до типу енкодерів, які призначені для вказівки напряму руху і / або кутового переміщення зовнішнього механізму. Покроковий енкодер формує імпульси, кількість яких відповідає повороту вала на певний кут. Цей тип енкодерів, на відміну від абсолютних, не формує код положення вала, коли вал знаходиться в спокої.
Покроковий енкодер пов'язаний з рахунковим пристроєм, це необхідно для підрахунку імпульсів і перетворення їх в міру переміщення вала.
Покроковий енкодер пов'язаний з рахунковим пристроєм, це необхідно для підрахунку імпульсів і перетворення їх в міру переміщення вала.
Диск імпульсного енкодера виготовленого на кафедрі "Локомотиви"
Квадратура виходу (виходи А і В)
Покроковий оптичний енкодер складається з наступних компонентів: джерела світла, диска з мітками, фототранзісторной збірки і схеми обробки сигналу. Диск покрокового енкодера поділені на точно позиційований позначки. Кількість відміток визначає кількість імпульсів за один оборот. Наприклад, якщо диск поділений на 1000 міток, тоді за 250 імпульсів вал повинен повернутися на 90 градусів.
Покроковий оптичний енкодер складається з наступних компонентів: джерела світла, диска з мітками, фототранзісторной збірки і схеми обробки сигналу. Диск покрокового енкодера поділені на точно позиційований позначки. Кількість відміток визначає кількість імпульсів за один оборот. Наприклад, якщо диск поділений на 1000 міток, тоді за 250 імпульсів вал повинен повернутися на 90 градусів.
Зовнішній вигляд енкодера
Диск з мітками енкодера
Принцип роботи енкодера
Для квадратури виходу енкодера використовуються два вихідних каналу, для того щоб визначити - обертається вал за годинниковою стрілкою або проти годинникової стрілки, засноване на зсуві фази 90 ° ± 0 °, допуск ± 45 ° - прийнятний для специфікації зсуву фази. Енкодер з єдиним виходом (A) більш відомий як тахометр.
При обертанні датчик формує імпульси, за якими приймаючий пристрій визначає поточне положення координати шляхом підрахунку кількості імпульсів лічильником. Для прив’язки системи відліку інкрементальні датчики мають референтну мітку («маркер»), одну за оберт, через яку потрібно пройти після включення обладнання.
Для визначення відстані та напрямку переміщення застосовуються два канали («синус» та «косинус», що позначаються у документації зазвичай якA та B), в яких ідентичні послідовності імпульсів зміщені на 90° відносно один одного, що дозволяє визначати напрямок обертання у кутових датчиках. Крім каналів «синус» та «косинус» у сучасних енкодерах використовуються також сигнал «мітка за оберт» («маркер», референтна мітка, позначена як Z, C або R ), який дозволяє визначити точне положення «нуля» координати приводу.
Рис. 1.22. Схема формування сигналу інкрементальний енкодером
В якості приймаючого пристрою виступає прилад на базі мікроконтролера зі влаштованим модулем захвату даних. Швидкість обертання визначається шляхом підрахунку часу між імпульсами інкрементального датчика, для цього блок захвату даних налаштовано таким чином, що при фронті вхідного сигналу з інкрементального датчика зберігається час t1, який при наступному фронті віднімається з захопленого часу t2, це і буде час між двома імпульсами, час t2 зберігається для наступного вимірювання і т. д.
Рис. 1.23. Визначення часу між імпульсами
Для зручності використання приладу та наглядного відображення швидкостей валу двигуна вирішено ряд швидкостей, що отримані приладом візуалізувати з допомогою графіка даних на ПК оператора.
Максимальна частота відповіді
Максимальна частота відповіді є частотою, при якій обертається енкодер може дати електричний відповідь. Тактова частотароздільна здатність має відношення до кількості вихідних імпульсів, на які енкодер реагує в секунду. Отже, енкодер покрокового типу повинен задовольнити наступне відношення:
(Rpm / 60) x (роздільна здатність) ≤ максимальної частоти відповіді.
Покажчик нульової позначки / імпульс повного обороту (вихід N)
У енкодера, що має цей вихід, імпульс на цьому виході з'являється в кожному обороті вала. Функція показника нуля може використовуватися для скидання зовні пов'язаного лічильника або для реєстрації початкової (нульовий) позиції.
Роздільна здатність
- це кількість вихідних імпульсів за обертання валу.
Максимальна частота відповіді є частотою, при якій обертається енкодер може дати електричний відповідь. Тактова частотароздільна здатність має відношення до кількості вихідних імпульсів, на які енкодер реагує в секунду. Отже, енкодер покрокового типу повинен задовольнити наступне відношення:
(Rpm / 60) x (роздільна здатність) ≤ максимальної частоти відповіді.
Покажчик нульової позначки / імпульс повного обороту (вихід N)
У енкодера, що має цей вихід, імпульс на цьому виході з'являється в кожному обороті вала. Функція показника нуля може використовуватися для скидання зовні пов'язаного лічильника або для реєстрації початкової (нульовий) позиції.
Роздільна здатність
- це кількість вихідних імпульсів за обертання валу.
Для механічного з'єднання вала датчика із зовнішнім механізмом слід використовувати спеціальний перехідник (зчеплення) гнучкого типу, який призначений для компенсації можливого биття валів, як в радіальному, так і в осьовому напрямку. Це дозволяє різко знизити ймовірність передчасного зносу підшипників вала датчика. Уже незначний, що виник в осьовому напрямку валу, люфт може привести до повного електричної відмови енкодера. Це пов'язано з тим, що для досягнення високого дозволу, оптичний диск і зчитує матриця розташовуються в безпосередній близькості один від одного і мінімальне осьове биття вала може привести до їх механічного контакту, що надалі приведе до руйнування нанесених на диск міток.
Датчик тиску - це прилад, за допомогою якого змінюється тиск виміряють середовища (рідини, газів і пари), завдяки зміні особистих фізичних параметрів. Тиск вимірюючого середовища в датчиках реформується в стандартизовані пневматичні електронні сигнали, або в цифровий код. Датчики тиску широко використовуються в системах керівництва технологічними процесами, оскільки тиск є одним з основних величин більшості виробничих процесів.
Також, датчики тиску часто використовуються для вимірювання тиску в агресивному середовищі. Якщо говорити про стандартні датчики, то вони створені вимірювати абсолютний, надлишковий і диференціальний тиск у всілякій амплітуді. Також вони можуть вимірювати витрати рідини і її рівень. Датчики тиску використовуються буквально у всіх промислових сферах, включаючи і енергетику.
Кожна модель датчиків тиску, яку випускає виробник, відрізняється одна від одної варіацією електричних і механічних з'єднань, вихідним сигналом, присутністю в ній дисплея / радіатора / роздільника і т. ін. Але, при цьому, спосіб роботи датчика однієї моделі і базові конструкторські впровадження повністю однакові, не залежно від терміну давності виконання моделі.
Головним елементом у всіх датчиках тиску є пружний елемент. Саме він несе відповідальність за точність вимірювання, термін служби приладу і його надійність. У каталозі компанії «Danfoss» Ви зможете знайти відповідний датчик з найбільшою точністю і потрібними габаритами.
Перетворювачі тиску
Перетворювачі тиску необхідні для перетворення значення тиску (абсолютного, надлишкового або диференціального). Також даний прилад дозволяє змінити значення рівня в струмовий стандартизований вихідний сигнал і цифровий сигнал по базі протоколу HART. Перетворювачі тиску також можуть стандартизувати витрати газу і рівень рідини.
Да́тчик ти́ску (вимі́рювальний перетво́рювач ти́ску) — пристрій, що дозволяє отримувати і дистанційно передавати сигнал, що відповідає вимірюваному тиску.
Прилади, що поєднують у собі датчик тиску та засіб відображення значення тиску і призначені для вимірювання надлишкового тиску називаються манометрами, або напоромірами, для вимірювання вакуумметричного тиску (нижче атмосферного, розрідження) — вакуумметрами або тягомірами, для одночасного вимірювання надлишкового і вакуумметричного тиску — мановакуумметрами або тягонапорометрами.
Манометри виконують функцію локального контролю і у більшості випадків через відсутність дистанційного доступу до їх показів (за виключенням манометрів з уніфікованим вихідним електричним сигналом) не можуть використовуватись у сучасних засобах автоматизації. Ця функція покладається на вимірювальні перетворювачі тиску.
Класифікація
Ці прилади класифікуються за видом тиску, що вимірюється і типом вихідного сигналу. Вимірювальні перетворювачі тиску розрізняються також, по одиницях вимірювання та за низкою основних технічних характеристик (ГОСТ 22520-85[1]).
За принципом роботи чи способом перетворення вимірюваного тиску у вихідний сигнал датчики тиску поділяються на:
- деформаційні (деформаційні переміщення пружного чутливого елемента (мембрани, сильфони, трубка Бурдона) трансформуються за посередництвом проміжних механізмів і перетворювачів в електричний чи електромагнітний сигнал);
- електричні (вимірюваний тиск, впливаючи на чутливий елемент, змінює його власні електричні параметри: електричний опір, електричну ємність або електричний заряд, котрі стають мірою цього тиску).
В останні роки набули поширення і інші принципи створення вимірювальних перетворювачів тиску: волоконно-оптичні, гальваномагнітні, об'ємного стиску, акустичні, дифузійні та ін.
За видом вимірюваного тиску датчики тиску поділяються на:
- перетворювачі абсолютного тиску;
- перетворювачі надлишкового тиску;
- перетворювачі вакуумметричного тиску;
- перетворювачі надлишкового/вакуумметричного тисків;
- перетворювачі різниці тисків;
- перетворювачі гідростатичного тиску.
За видом вихідного сигналу датчики тиску поділяються на:
- аналогові (вимірюваний тиск перетворюється в аналоговий уніфікований пневматичний чи електричний сигнал);
- цифрові.
Основні діючі датчики тиску належать до аналогових з уніфікованим струмовим сигналом 0…5, 0…20 або 4…20 мА. Останніми роками спостерігається перехід до цифрових датчиків тиску (у тому числі поширення набуває цифровий протокол HART). Бурхливо розвивається системна інтеграція перетворювачів тиску з використанням окремих різновидностей промислових мереж (Modbus, Profibus та ін.). При цьому використовується цифровий протокол обміну інформацією між давачем тиску та системою керування, що суттєво спрощує взаємозамінність приладів різних виробників.
Деформаційні датчики тиску
У промисловій практиці вимірювання тисків поширення набули деформаційні прилади з пружним чутливим елементом. У цих приладах тиск визначається за деформацією пружних чутливих елементів або за зусиллям, що вони створюють, котрі перетворюються передавальними механізмами в кутове чи лінійне переміщення вказівника на шкалі приладу. За видом пружного чутливого елемента пружинні прилади поділяються на такі види:
Електричні датчики тиску
В електричних датчиках тиску вимірюваний тиск, здійснюючи вплив на чутливий елемент, змінює його власні електричні параметри: електричний опір, електричну ємність чи електричний заряд, котрі стають мірою цього тиску. Основна маса датчиків тиску реалізовані за одним із трьох принципів:
- ємнісні — використовують пружний чутливий елемент у вигляді конденсатора із змінним зазором за рахунок зміщення чи прогину під дією тиску рухомого електрода-мембрани відносно нерухомого електрода;
- п'єзоелектричні — базуються на залежності поляризованого заряду чи резонансної частоти п'єзокристала кварцу чи турмаліну під дією прикладеного до нього тиску;
- тензорезисторні — використовують залежність активного електричного опору провідника чи напівпровідника від ступеня його деформації.
Принципи реалізації
Датчик тиску складається з первинного перетворювача тиску, у склад якого входить чутливий елемент з приймачем тиску, схема вторинної обробки та пристрій виводу, розміщені у корпусі. Основною відмінністю таких приладів є точність реєстрації тиску, яка залежить від принципу перетворення тиску в електричний сигнал: тензометричний, п'єзорезистивних, ємнісний, індуктивний, резонансний, іонізаційний.
Тензометричний метод
Робота чутливих елементів датчиків базується на принципі вимірювання зміни опору тензорезисторів, приклеєних до титанової мембрани в умовах деформації під дією тиску.
Набули поширення дротові і фольгові тензорезистори, що виготовляють із провідників типу манганіну, ніхрому, константану, а також напівпровідникові тензорезистори, що виготовляють із кремнію та германію. Опір тензорезисторів, що виготовляють із провідників, становить 30...500 Ом, а опір напівпровідникових тензорезисторів від 5•10-2...10 кОм.
Удосконалювання технології виготовлення напівпровідникових тензорезисторів створило можливість виготовляти тензорезистори безпосередньо на кристалічному елементі, виконаному із кремнію або сапфіру. Пружні елементи кристалічних матеріалів мають пружні властивості, що наближаються до ідеальних. Кремнієві перетворювачі мають високу часову і температурну стабільність. Для вимірювання тиску чистих неагресивних діелектриків застосовуються вирішення, що юазуються на використанні чутливих елементів або без покриття, або з захистом силіконовим гелем. Для вимірювання тиску агресивних середовищ і у більшості промислових застосуваннях використовується перетворювач тиску в герметичному метало-скляному корпусі, з роздільною діафрагмою з нержавіючої сталі, що передає тиск вимірюваного середовища за допомогою кремнійорганічної рідини.
Класи точності тензорезисторних вимірювальних перетворювачів надлишкового тиску, вакууму та різниці тисків 0,6; 1,0; 1,5.
Діапазони вимірювання:
- надлишкового тиску — від 0...10-3 до 0...60 МПа;
- розрідження -1...0 кПа;
- абсолютного тиску — від 0...2,5 кПа до 0...2,5МПа;
- різниці тисків — від 0...1 кПа до 0...2,5МПа.
П'єзоелектричний метод
П'єзоелектричні вимірювальні перетворювачі тиску. В основу роботи цих перетворювачів покладене перетворення вимірювального тиску в зусилля за допомогою деформаційного чутливого елемента і наступного перетворення цього зусилля в сигнал вимірювальної інформації п'єзоелектричним перетворювальним елементом. Принцип дії п'єзоелектричного перетворювального елемента заснований на п'єзоелектричному ефекті, який спостерігається в ряді кристалів, таких, як кварц, турисін, титанат барію і ін. Суть п'єзоелектричного ефекту полягає в тому, що якщо кварцові пластини Х-зрізу піддати стиску силою N, то на її поверхні виникнуть заряди різних знаків. Значення заряду Q пов'язане із силою N співвідношенням
де k — п'єзоелектрична постійна, котра не залежить від розміру пластини і визначається природою кристалу.
вимірювальні перетворювачі цього типу мають високі динамічні характеристики, що обумовило їхнє широке застосування при контролі тиску в системах зі швидкопротікаючими процесами. Чутливість п'єзоелектричних вимірювальних перетворювачів тиску може бути підвищена шляхом застосування декількох, паралельно включених кварцових пластин і збільшення ефективної площі мембрани.
Верхні межі вимірювання п'єзоелектричних перетворювачів тиску із кварцовими чутливими елементами 2,5…100 МПа. Класи точності 1,5; 2,0. Через витік заряду із кварцових пластин перетворювачі тисків цього типу не використовують для вимірювання статичних тисків.
Ємнісний метод
Ємнісні сенсори використовують метод зміни ємності конденсатора при зміні відстані між обкладками. Відомі керамічні або кремнієві ємнісні сенсори тиску і сенсори, виконані з використанням пружної металевої мембрани. При зміні тиску мембрана з електродом деформується і відбувається зміна ємності. В елементі з кераміки або кремнію, простір між обкладками зазвичай заповнений маслом або іншою органічною рідиною. Недолік - нелінійна залежність ємності від прикладеного тиску.
Резонансний метод
В основі методу лежать хвильові процеси: акустичні або електромагнітні. Це і пояснює високу стабільність датчиків і високі вихідні характеристики приладу.
Частковим прикладом може служити кварцовий резонатор. При прогині мембрани, відбувається деформація кристалу кварцу, підключеного в електричну схему і його поляризація. У результаті зміни тиску частота коливань кристала змінюється. Підібравши параметри резонансного контуру, змінюючи ємність конденсатора або індуктивність котушки, можна домогтися того, що опір кварцу падає до нуля - частоти коливань електричного сигналу і кристала збігаються - настає резонанс.
До недоліків можна віднести індивідуальну характеристику перетворення тиску, значний час відгуку, неможливість проводити вимірювання в агресивних середовищах без втрати точності показів приладу.
Індукційний метод
Індукційний спосіб базується на реєстрації вихрових струмів (струмів Фуко). Чутливий елемент складається з двох котушок, ізольованих між собою металевим екраном. Перетворювач вимірює зміщення мембрани за відсутності механічного контакту. У котушках генерується електричний сигнал змінного струму таким чином, що заряд і розряд котушок відбувається через однакові проміжки часу. При відхиленні мембрани створюється струм у зафіксованій основній котушці, що призводить до зміни індуктивності системи. Зсув характеристик основний котушки дає можливість перетворити тиск у стандартизований сигнал, прямо пропорційний прикладеному тиску.
Перевагою такої системи, є можливість вимірювання низьких надлишкових і диференціальних тисків, досить висока точність і незначна температурна залежність. Однак датчик чутливий до магнітних впливів, що пояснюється наявністю котушок, які при проходженні змінного сигналу створюють магнітне поле.
Іонізаційний метод
В основі лежить принцип реєстрації потоку іонізованих частинок. Аналогом є лампові діоди. Лампа оснащена двома електродами: катодом і анодом, - нагрівачем а також. У деяких лампах останній відсутній, що пов'язано з використанням досконаліших матеріалів для електродів. Корпус лампи виконаний з високоякісного скла.
Перевагою таких ламп є можливість реєструвати низький тиск - аж до глибокого вакууму з високою точністю. Однак слід суворо враховувати, що подібні прилади не можна експлуатувати, якщо тиск у камері близький до атмосферного. Тому подібні перетворювачі необхідно поєднувати з іншими датчиками тиску, наприклад, ємнісними. Крім іншого, іонізаційні лампи повинні оснащуватися додатковими приладами, оскільки залежність сигналу від тиску є логарифмічною.
Прилади
рис.1 Манометр Бурдона
Інструменти, використовувані для вимірювання тиску називаються манометри і вакуумметри.
Манометр - це прилад для вимірювання тиску рідин і газів.
Вакуумметр (вакуум-манометр) — прилад для вимірювання тиску розріджених газів або для вимірювання глибини вакууму: різниці між атмосферним тиском і тиском розрідженого газу. Поширені теплові вакуум-манометри, зокрема з термопарами, дія яких ґрунтується на залежності теплопровідності газу від тиску.
Електронні датчики тиску
Тиск датчик - вимірювальний перетворювач тиску рідини або газу в електричний, пневматичний та іншого вигляду вихідний сигнал. Служить також для виміру розрядок і перепаду тиску. На тиск до 10Мн/м2( 100 кгс/см2 ) і вище. Тиск датчики будують за принципом прямого перетворення вимірюваного тиску в зусилля і потім у вихідний електричний сигнал наприклад п'єзоелектричні датчики, магнітопружні датчики. Для виміру відносно малого тиску, тиск датчики будують з проміжними і крайовими перетворювачами. Проміжними можуть служити рідинні манометричні перетворювачі, пружини мембрани, сильфони і ін. Як крайові застосовують реостатні, індуктивні, ємкісні перетворювачі.
рис.2 Принципова схема датчика тиску компенсаційного типа: а — електричній силовій компенсації; б — пневматичній силовій компенсації.
Існують тиск датчики, що працюють на принципі електричної або пневматичної силової компенсації. Зусилля Р(див рис.2), що створюється вимірюваним тиском на чутливий елемент 1 , через систему важеля 2 врівноважується силовим пристроєм 3 зворотному зв'язку. При зміні тиску керівник елемент 4 індикатора розузгодження 5 відхиляється від свого первинного нульового положення. Сигнал розузгодження, що формується при цьому в індикаторі 5, посилюється в підсилювачі 6 і у вигляді вихідного струму i вих (або тиск Рвих ) поступає в пристрій 3 і на відліковий пристрій 7. Вихідний сигнал змінюється до тих пір, поки що розвивається в пристрої 3 силове протидію не зрівноважить вимірюваний тиск. У момент рівноваги елементи 2 і 4 повертаються в первинне положення. Рпіт — тиск в живлячій мережі. Вимір перепаду тиску здійснюють диференціальним (різницевим), мембранним, сільфоном або рідинним манометричним датчиком.
рис.3 Схема пристрою п'єзоелектричного датчика тиску: p — вимірюваний тиск; 1 — пьезопластіни; 2 — гайка з діелектрика; 3 — електричний вивід; 4 — корпус (службовець другим виводом); 5 — ізолятор; 6 — металевий електрод.
П'єзоелектричний датчик - вимірювальний перетворювач механічного зусилля в електричний сигнал; його дія заснована на використанні п'єзоелектричного ефекту (див. рис3 ). Один з варіантів конструкції п'єзоелектричного датчика тиску показаний на рис . Під дією вимірюваного тиску на зовнішній і внутрішній сторонах пари пластин пьезоелектрика виникають електричні заряди, причому сумарна ерс(електрорушійна сила) (між виводом і корпусом) змінюється пропорційно тиску. П'єзоелектричний датчик доцільно застосовувати при вимірі бистрозмінюючого тиску; якщо тиск міняється повільно, то зростає погрішність перетворення із-за «стікання» електричного заряду з пластин на корпус. Включенням додаткового конденсатора паралельно п'єзоелектричного датчика, можна зменшити погрішність виміру, проте при цьому зменшується напруга на виводах датчика. Основні достоїнства п'єзоелектричних датчиків — їх високі динамічні характеристики і здатність сприймати коливання тиску з частотою від десятків гц до десятків Мгц. Застосовуються при тензометричних вимірах, у вагових і сортувальних (по вазі) пристроях, при вимірах вібрацій і деформацій і т.д.
Магнітопружний датчик(магнітострикційний датчик) - вимірювальний перетворювач механічних зусиль (деформацій) або тиску в електричний сигнал. Дія магнітопружного датчика заснована на використанні залежності магнітних характеристик деяких матеріалів (наприклад, пермалою, інвару ) від механічної напруги в них. Робочий елемент магнітопружного датчика — магнітопровід, на якому розміщено одна або декілька обмоток, що включаються в міст вимірник. Магнітопровід магнітопружного датчика укріплюють на поверхні деталі (або споруди) у напрямі зусиль, що діють, або деформацій. Зміни магнітних характеристик, зокрема магнітній проникності матеріалу магнітопровода, виявляються в зміні індуктивності або взаїмоїндуктівності обмоток. Магнітопружний датчик найдоцільніше застосовувати при вимірах малих деформацій (як постійних, так і бистропеременних) в твердих тілах, а також вимірах тиску рідин і газів, коли потрібна висока чутливість вимірів при відносно малої їх точності.
Розрізняють такі типи датчиків вологості: ємнісні датчики відносної вологості(RH)і датчики точки роси, резистивні датчики вологості і теплопровідні датчики абсолютної вологості. Загальні принципи роботи кожного типу датчиків можна при бажанні знайти на наукових сайтах і журналах. Не думаю, що має сенс заглиблюватися в досить складні для звичайного споживача терміни, графіки і формули. А тим, хто має бажання в загальних рисах дізнатися переваги того або іншого типу датчиків, наведу таку інформацію у вигляді невеликої порівняльної таблиці.
Таблиця переваг різних типів датчиків вологості
Ємнісні датчики
|
Резистивні датчики
|
Теплопровідні датчики
|
Широкий діапазон вимірювань
Взаємозамінність при лазерній обробці
Стійкість до конденсату
|
Взаємозамінність
Невисока ціна
Можливість віддаленого використання
|
Можливість застосування в корозійному середовищі і при високих температурах
|
Найбільш зручними в експлуатації по праву вважаються цифрові датчики вологості, обладнані чутливими змінними головками. В основу роботи цих приладів належать їх електричні властивості — опір та ємність. Давайте докладніше розглянемо, як працює цифровий датчик вологості. Більш точний результат вимірювання температури і вологості в порівнянні з іншими аналогами, цифровий датчик вологості дає завдяки вбудованому влагочувствительному конденсатору і процесора. Влагочувствительный елемент являє собою пластину з впаяними електродами, а покрита вона гігроскопічним полімером, який збирає з повітря молекули води, тим самим змінюючи ємність конденсатора. Значення температури і вологості розраховуються за допомогою спеціальної голівки, яка проходить калибрацию на заводі виробника. Усі потрібні значення для обчислень зберігаються в пам’яті вимірює головки. Така будова і принцип роботи цифрового датчика дозволяє без праці і досить швидко замінити головку. Що стосується обчислення температури точки роси і значення відносної вологості то цим займається вбудований процесор , використовуючи фізичні формули.
Крім того, датчики вологості можуть бути бездротовими і стаціонарними. Бездротові датчики більш зручні та знімати показники з них набагато простіше, вони не псують своїми проводами інтер’єр, але і вартість таких датчиків, природно, вище, ніж стаціонарних. Висока ціна пояснюється більш дорогими і складними технологіями передачі інформації на відстані, які використовуються при виготовленні бездротових датчиків. Існує два варіанти можливої передачі інформації з датчика:
- Передаються всі конкретні показники
- Передається тільки отриманий результат( повідомляється яка вологість у даний період часу знижена або підвищена)
Датчик струму і напруги дозволяє вирішувати цю задачу дистанційно. Ця функція застосовується в електроніці, електротехніці, енергетиці, при діагностиці ланцюгів, для визначення величини струмів, управління запуском схем захисту, при виявленні відмов
Датчики струму і напруги
У сучасній електротехнічної промисловості дуже важливим є якісне дистанційне вимірювання струмів. Датчик струму і напруги дозволяє вирішувати цю задачу дистанційно. Ця функція застосовується в електроніці, електротехніці, енергетиці, при діагностиці ланцюгів, для визначення величини струмів, управління запуском схем захисту, при виявленні відмов у працюючому обладнанні. При всьому різноманітті способів вимірів можна виділити три найбільш часто використовуваних:
1. Резистивний.
2. Заснований на використанні ефекту Холла.
3. Заснований на застосуванні трансформаторів струму.
Спосіб, з використанням трансформаторів струму може бути застосований лише до змінного струму. Всі три типи датчиків не позбавлені недоліків, які обмежують їх сфери застосування. Датчики, засновані на законі Ома (резистивні) - найдоступніші і точні при відносно невеликих токах. Однак при збільшенні струму, що проходить через датчик, відбувається його значний розігрів, що вимагає застосування більш потужних резисторів, які мають паразитне індуктивність. Все це знижує точність вимірювань. При застосуванні малоіндуктівних резисторів підвищуються витрати, але з'являється можливість вимірювання струмів аж до одиниць мегагерц. Але, крім цього, після зняття напруги з вимірювального резистору, його необхідно обробити, посилити і т.д., що здійснюється електронними підсилювачами. Ці пристрої дуже чутливі до електромагнітним наведенням від ланцюгів з протікає по них великим струмом, що також спотворить результат вимірювань. Крім цього, такі схеми вимірювань не мають гальванічної розв'язки.
Ефект Холла був відкритий ще в минулому столітті. Сенс його полягає в тому, що якщо відрізок напівпровідника помістити перпендикулярно в магнітне поле, то на його кінцях з'явиться різниця потенціалів. Такі датчики не впливають на вимірювану ланцюг. Перші датчики, придатні для використання в промисловості на основі цього ефекту були виготовлені тільки в 60х роках двадцятого століття. Вони мали інтегральне або гібридне виконання, але були дороги, оскільки сама технологія напівпровідників ще тільки робила перші кроки щодо здешевлення своєї продукції. Тільки до 90 років напівпровідникова промисловість накопичила необхідний технологічний потенціал, що дозволив почати масовий випуск спеціалізованих мікросхем, що використовують у своїй роботі також і ефект Холла. Стали доступними такі спеціалізовані пристрої, як датчик постійного і змінного струму і т.д.
Шунт - пристрій, що дозволяє електричному струму протікати в обхід якої-небудь ділянки схеми, звичайно являє собою низькоомний резистор.
Рисунок 7.2 Малоамперний шунт
Шунти випускаються на діапазон струмів від 0,5А до 10кА і нормовані за вихідною напругою 30, 50, 75, 100 і 150 мВ. Найбільш поширені шунти на 75 мВ. Через значний вплив власної індуктивності, скін-ефекту і наведення на вимірювальний контур шунти використовуються в основному, для вимірювання постійного струму.
Датчики температури. Типи датчиків, їх характеристики. Приклади використання.
Датчики температури
Більшість технологічних процесів йде зараз по шляху автоматизації. Крім того, управління численними механізмами і агрегатами, а часто і машинами просто немислимо без точних вимірювань всіляких фізичних величин. Важливим є вимір тиску, вимірювання кутової швидкості, а також лінійної і багато-багато інших. Але найпоширенішими (близько 50%) є температурні виміри. Приміром, середня за величиною атомна станція налічує приблизно 1500 контрольних (вимірювальних) точок, а велике хімвиробництво, налічує таких вже близько 20 тис.
Так як діапазон вимірювань і їх умови можуть сильно відрізняться один від одного, розроблені різні по точності, стійкості , швидкодії типи датчиків (і первинних перетворювачів). Якого б типу не був температурний датчик, загальним для всіх є принцип перетворення. А саме: вимірювана температура перетворюється в електричну величину (якраз за це і відповідає первинний перетворювач). Це обумовлено тим, що електричний сигнал просто передавати на великі відстані (висока швидкість прийому-передачі), легко обробляти (висока точність вимірів) і, нарешті, швидкодія.
Далі, пропонуємо вам ознайомитися з різними видами датчиків температури, а в кінці статті з список питань які необхідно вирішити перед покупкою датчика температури.
Види датчиків температури, за типом дії
Терморезистивні термодатчики
Терморезистивні термодатчики - засновані на принципі зміни електричного опору (напівпровідника або провідника) при зміні температури. Розроблені вони були вперше для океанографічних досліджень. Основним елементом є терморезистор - елемент змінює свій опір залежно від температури навколишнього середовища.
Так як діапазон вимірювань і їх умови можуть сильно відрізняться один від одного, розроблені різні по точності, стійкості , швидкодії типи датчиків (і первинних перетворювачів). Якого б типу не був температурний датчик, загальним для всіх є принцип перетворення. А саме: вимірювана температура перетворюється в електричну величину (якраз за це і відповідає первинний перетворювач). Це обумовлено тим, що електричний сигнал просто передавати на великі відстані (висока швидкість прийому-передачі), легко обробляти (висока точність вимірів) і, нарешті, швидкодія.
Далі, пропонуємо вам ознайомитися з різними видами датчиків температури, а в кінці статті з список питань які необхідно вирішити перед покупкою датчика температури.
Види датчиків температури, за типом дії
Терморезистивні термодатчики
Терморезистивні термодатчики - засновані на принципі зміни електричного опору (напівпровідника або провідника) при зміні температури. Розроблені вони були вперше для океанографічних досліджень. Основним елементом є терморезистор - елемент змінює свій опір залежно від температури навколишнього середовища.
Безперечні переваги термодатчиків цього типу це довготривала стабільність, висока чутливість, а також простота створення інтерфейсних схем.
На зображенні наведено датчик 702-101BBB-A00, діапазон вимірювання якого від -50 до +130 ° С. Цей датчик ставитися до групи кремнієвих резистивних датчиків (що це таке читайте двома абзацами нижче). Зверніть увагу, на його розміри. Виробляє цей датчик фірма Honeywell International
В залежності від матеріалів використовуваних для виробництва терморезистивного датчиків розрізняють:
Резистивні детектори температури (РДТ). Ці датчики складаються з металу, найчастіше платини. В принципі, будь який метал змінює свій опір під впливом температури, але використовують платину так як вона володіє довготривалою стабільністю, міцністю і відтворюваністю характеристик. Для вимірювань температур понад 600 ° С може використовуватися також вольфрам. Мінусом цих датчиків є висока вартість і нелінійність характеристик.
Кремнієві резистивні датчики. Переваги цих датчиків-хороша лінійність і висока довготривала стабільність. Також ці датчики можуть вбудовуватися прямо в мікроструктури.
Термістори. Ці датчики виготовляються з метал-оксидних сполук. Датчик вимірює тільки абсолютну температуру. Істотним недоліком термісторів є необхідність їх калібрування та велика нелінійніст, а також старіння, однак при проведенні всіх необхідних настройок можуть використовуватися для прецизійних вимірювань.
Напівпровідникові
В якості прикладу зображено напівпровідниковий датчик температури LM75A, що випускається фірмою NXP Semiconductors. Діапазон вимірювань цього датчика від -55 до +150.
Напівпровідникові датчики реєструють зміна характеристик pn переходу під впливом температури. В якості термодатчиків можуть бути використані будь які діоди або біполярні транзистори. Пропорційна залежність напруги на транзисторах від абсолютної температури (в Кельвінах) дає можливість реалізувати досить точний датчик.
Переваги таких датчиків - простота і низька вартість, лінійність характеристик, маленька похибка. Крім того, ці датчики можна формувати прямо на кремнієвій підкладці. Все це робить напівпровідникові датчики дуже затребуваними.
Термоелектричні (термопари)
Термоелектричні перетворювачі - інакше, термопари. Вони діють за принципом термоелектричного ефекту, тобто завдяки тому, що в будь-якому замкнутому контурі (з двох різнорідних напівпровідників або провідників) виникая електричний струм, у разі якщо місця зпайки відрізняються по температурі. Так, один кінець термопари (робочий) занурений в середовище, а інший (вільний) - незанурений. Таким чином, виходить, що термопари це відносні датчики і вихідна напруга буде залежати від різниці температур двох частин. І майже не буде залежати від абсолютних їх значень.
Термоелектричні перетворювачі - інакше, термопари. Вони діють за принципом термоелектричного ефекту, тобто завдяки тому, що в будь-якому замкнутому контурі (з двох різнорідних напівпровідників або провідників) виникая електричний струм, у разі якщо місця зпайки відрізняються по температурі. Так, один кінець термопари (робочий) занурений в середовище, а інший (вільний) - незанурений. Таким чином, виходить, що термопари це відносні датчики і вихідна напруга буде залежати від різниці температур двох частин. І майже не буде залежати від абсолютних їх значень.
Виглядати термопара може так, як показано на малюнку. Це термопара ДТПКХХ4, вона вимірює температуру в межах від -40 до +400.
Діапазон вимірюваних з їх допомогою температур, від -200 до 2200 градусів, і прямо залежить від використовуваних в них матеріалів. Наприклад, термопари з неблагородних металів - до 1100 ° С. Термопари із благородних металів (платинова група) - від 1100 до 1600 градусів. Якщо необхідно провести виміри температур понад цього, використовуються жаростійкі сплави (основою служить вольфрам). Як правило використовується в комплекті з мілівольтметром, а вільний кінець (конструктивно виведений на голівку) віддалений від вимірюваного середовища за допомогою подовжуючого проводу. Одним з недоліків термопари є досить велика похибка. Найбільш поширеним способом застосування термопар є електронні термометри.
Пірометри
Пірометри - безконтактні датчики, які реєструють випромінювання виходить від нагрітих тіл. Основною перевагою пірометрів (на відміну від попередніх температурних датчиків) є відсутність необхідності поміщати датчик безпосередньо в контрольоване середовище. В результаті такого занурення часто відбувається спотворення досліджуваного температурного поля, не кажучи вже про зниження стабільності характеристик самого датчика.
Розрізняють три види пірометрів:
Флуоресцентні. При вимірюванні температури за допомогою флуоресцентних датчиків на поверхню об'єкта, температуру якого необхідно виміряти, наносять фосфорні компоненти. Потім об'єкт піддають впливу ультрафіолетового імпульсного випромінювання, в результаті якого виникає післявипромінювання флуоресцентного шару, властивості якого залежать від температури. Це випромінювання детектується і аналізується.
Інтерферометричні. Інтерферометричні датчики температури базуються на порівнянні властивостей двох променів - контрольного та пропущеного через середовище, параметри якої змінюються в залежності від температури. Чутливим елементом цього типу датчиків найчастіше виступає тонкий кремнієвий шар, на коефіцієнт заломлення якого, а, відповідно, і на довжину шляху променя, впливає температура.
Датчики на основі розчинів, що міняють колір при температурному впливі. У цьому типі датчиків-пірометрів застосовується хлорид кобальту, розчин якого має тепловий зв'язок з об'єктом, температуру якого необхідно виміряти. Коефіцієнт поглинання видимого спектру у розчину хлориду кобальту залежить від температури. При зміні температури змінюється величина пройшовшого розчин світла.
Акустичні
Акустичні термодатчики - використовуються переважно для вимірювання середніх і високих температур. Акустичний датчик побудований на принципі того, що в залежності від зміни температури, змінюється швидкість поширення звуку в газах. Складається з випромінювача і приймача акустичних хвиль (просторово рознесених). Випромінювач випускає сигнал, який проходить через досліджувану середу, в залежності від температури швидкість сигналу змінюється і приймач після отримання сигналу вираховує цю швидкість.
Використовуються для визначення температур, які не можна виміряти контактними методами. Також застосовуються в медицині для неінвазивного (без операційного проникнення всередину тіла хворого) вимірювання глибинної температури, наприклад, в онкології. Недоліками таких вимірювань є те, що при дотику вони можуть викликати відповідні фізіологічні реакції, що в свою чергу спричиняє спотворення вимірювання глибинної температури. Крім того, можуть виникати відображення на межі «датчик-тіло», що також здатне викликати похибки.
П'єзоелектричні
У датчиках цього типу головним елементів є кварцовий п'єзорезонатор.
Як відомо п'єезоматеріал змінює свої розміри при впливі струму (прямий п'єзоефект). На цей п'єзоматеріал поперемінно передається напруга різного знаку, від чого він починає коливатися. Це і є п'єзорезонатор. З'ясовано, що частота коливань цього резонатора залежить від температури, це явище і покладено в основу п'єзоелектричного датчика температури.
На що необхідно звернути увагу при виборі датчиків температури
Температурний діапазон.
Чи можна занурювати датчик у вимірюване середовище або об'єкт? Якщо розташування всередині середовища неприпустимо, то варто вибирати акустичні термометри і пірометри.
Які умови вимірювань!? Якщо використовується агресивне середовище, то необхідно використовувати або датчики в корозійнозахищених корпусах, або використовувати безконтактні датчики. Крім того, необхідно передбачити інші умови: вологість, тиск і тд.
Як довго датчик повинен буде працювати без заміни та калібрування. Деякі типи датчиків володіють відносно низькою довготривалої стабільністю, наприклад термістори.
Який вихідний сигнал необхідний. Деякі датчики видають вихідний сигнал у величині струму, а деякі автоматично перераховують його в градуси.
Інші технічні параметри, такі як: час спрацьовування, напруга живлення, дозвіл датчиків і похибка. Для напівпровідникових датчиків, важливим також являє тип корпусу.
Акустичні термодатчики - використовуються переважно для вимірювання середніх і високих температур. Акустичний датчик побудований на принципі того, що в залежності від зміни температури, змінюється швидкість поширення звуку в газах. Складається з випромінювача і приймача акустичних хвиль (просторово рознесених). Випромінювач випускає сигнал, який проходить через досліджувану середу, в залежності від температури швидкість сигналу змінюється і приймач після отримання сигналу вираховує цю швидкість.
Використовуються для визначення температур, які не можна виміряти контактними методами. Також застосовуються в медицині для неінвазивного (без операційного проникнення всередину тіла хворого) вимірювання глибинної температури, наприклад, в онкології. Недоліками таких вимірювань є те, що при дотику вони можуть викликати відповідні фізіологічні реакції, що в свою чергу спричиняє спотворення вимірювання глибинної температури. Крім того, можуть виникати відображення на межі «датчик-тіло», що також здатне викликати похибки.
П'єзоелектричні
У датчиках цього типу головним елементів є кварцовий п'єзорезонатор.
Як відомо п'єезоматеріал змінює свої розміри при впливі струму (прямий п'єзоефект). На цей п'єзоматеріал поперемінно передається напруга різного знаку, від чого він починає коливатися. Це і є п'єзорезонатор. З'ясовано, що частота коливань цього резонатора залежить від температури, це явище і покладено в основу п'єзоелектричного датчика температури.
На що необхідно звернути увагу при виборі датчиків температури
Температурний діапазон.
Чи можна занурювати датчик у вимірюване середовище або об'єкт? Якщо розташування всередині середовища неприпустимо, то варто вибирати акустичні термометри і пірометри.
Які умови вимірювань!? Якщо використовується агресивне середовище, то необхідно використовувати або датчики в корозійнозахищених корпусах, або використовувати безконтактні датчики. Крім того, необхідно передбачити інші умови: вологість, тиск і тд.
Як довго датчик повинен буде працювати без заміни та калібрування. Деякі типи датчиків володіють відносно низькою довготривалої стабільністю, наприклад термістори.
Який вихідний сигнал необхідний. Деякі датчики видають вихідний сигнал у величині струму, а деякі автоматично перераховують його в градуси.
Інші технічні параметри, такі як: час спрацьовування, напруга живлення, дозвіл датчиків і похибка. Для напівпровідникових датчиків, важливим також являє тип корпусу.
Основні поняття теорії цифрових автоматів. Алгебра логіки, цифровий автомат. Реалізація основних логічних функцій
Основні поняття теорії цифрових автоматів.
Математичний апарат, який описує дії дискретних пристроїв, базується на алгебрі логіки, її ще називають по імені автора – англійського математика Джорджа Буля (1815 – 1864) булевою алгеброю. Практичне застосування алгебри логіки першим знайшов американський вчений Клод Шеннон у 1938 р. при дослідженні електричних кіл з контактними вимикачами.
Для формального опису цифрових автоматів використовується апарат алгебри логіки. Логічною (булевою) змінною називається величина, яка може приймати тільки два значення 0 і 1. Сукупність різних значень змінних називаються набором. Основним предметом булевої алгебри є висловлювання – просте твердження, про яке можна стверджувати: істинне воно (позначають символом 1) або хибне (позначають символом 0).
Прості висловлювання позначають буквами, наприклад X X KX m , які у цифровій техніці називають змінними (аргументами).
У даний час головна задача алгебри логіки – аналіз, синтез і структурне моделювання будь-яких дискретних скінчених систем. Змінну із скінченим числом значень (станів) називають перемикальною, а з двома значеннями – булевою.
Операція – це чітко визначена дія над одним або декількома операндами, яка створює новий об’єкт (результат). У булевій операції операнди і результат набувають “булевого значення 1” і “булевого значення 0”.
Булеві функції можуть залежати від однієї, двох і в цілому n - змінних. Булева функція n – аргументів може мати до n N = 2 наборів.
Оскільки функції приймають тільки два значення. Отже, функція одного аргумента може мати чотири значення: y = x ; y = x ; y =1 (константа 1); y = 0 (константа 0). Два аргументи надають 16 значень функції.
Логічні функції двох змінних приведені в таблиці 1. Основними булевими операціями є заперечення (операція НЕ, інверсія), диз’юнкція (операція АБО, логічне додавання, об’єднання) і кон’юнкція (операція І, логічне множення).
Поняття цифрового автомата:в загальному випадку під цифровим автоматом можна розуміти модель типу «чорний ящик» яка характеризується великою кількістю вхідних сигналів Х, безліччю внутрішніх станів У і безліччю вихідних сигналів Z.
Рисунок - Загальне представлення цифрового автомату
Заперечення (Інакше - інверсія, операція НІ)
- це операція, вироблена над одним висловом, наприклад: Результат заперечення Р = 1 (істина), якщо А = 0 (брехня) і навпаки, що добре ілюструється так званої таблицею істинності Реалізується заперечення за допомогою інвертора.
Диз'юнкція (логічне додавання, операція АБО)
виробляється над двома або більше висловлюваннями, наприклад:. Результат диз'юнкції Р = 1 (ІСТИНА), якщо істинно хоча б одне з простих висловлювань.
Кон'юнкція. (Логічне множення, операція І)
виробляється над двома або більше висловлюваннями, наприклад: Результат кон'юнкції Р = 1 (ІСТИНА) тільки в разі, коли істинні всі прості висловлювання
Немає коментарів:
Дописати коментар